Multi-step hot-dip galvanizing passivation method
A hot-dip galvanizing and passivation solution technology, which is applied in the coating process of metal materials, can solve the problems of insufficient corrosion resistance, insufficient passivation film thickness, and insufficient passivation salt stability, and achieve the goal of slowing down the corrosion rate. Effect
- Summary
- Abstract
- Description
- Claims
- Application Information
AI Technical Summary
Problems solved by technology
Method used
Examples
Embodiment 1
[0027] 1) Prepare a rare earth passivation solution whose composition is Ce(NO 3 ) 3 : 0.001 mol / L; H 2 o 2 : 0.5 vol / L; Na 2 SO 4 : 0.5mol / L. Adjust the pH of the prepared passivation solution to 1, apply the passivation solution evenly on the galvanized sheet under constant temperature conditions, and cure at 100°C. Curing time: natural cooling for 2 hours.
[0028] 2) Reconstitute the molybdate passivation solution, the composition of which is Na 2 (MoO 4 )·2H 2 O: 4 g / L; ZrF 4 : 4 g / L; H 2 C 2 o 4 : 15 wt%. Adjust the pH to 3, apply the passivation solution evenly on the rare earth-treated galvanized panel, and cure at 150°C, curing time: natural cooling for 5 hours.
[0029] The prepared passivation film was tested for corrosion performance.
Embodiment 2
[0031] 1) Prepare a rare earth passivation solution whose composition is Ce(NO 3 ) 3 : 0.05 mol / L; H 2 o 2 : 2 vol / L; Na 2 SO 4 : 0.5 mol / L. Adjust the pH of the prepared passivation solution to 1, apply the passivation solution evenly on the galvanized panel under constant temperature conditions, and cure at 50°C. Curing time: natural cooling for 30 minutes.
[0032] 2) Reconstitute the molybdate passivation solution, the composition of which is Na 2 (MoO 4 )·2H 2 O: 20g / L; ZrF 4 : 8g / L; H 2 C 2 o 4 : 0.2 wt%. Adjust the pH to 4, apply the passivation solution evenly on the rare earth-treated galvanized plate, and cure at 150°C, curing time: natural cooling for 5 hours.
[0033] The prepared passivation film was tested for corrosion performance.
Embodiment 3
[0035] 1) Prepare a rare earth passivation solution whose composition is Ce(NO 3 ) 3 : 1 mol / L; H 2 o 2 : 0.05 / L; Na 2 SO 4 : 1 mol / L. Adjust the pH of the prepared passivation solution to 1, apply the passivation solution evenly on the galvanized panel under constant temperature conditions, and cure at 50°C. Curing time: natural cooling for 30 minutes.
[0036] 2) Reconstitute the molybdate passivation solution, the composition of which is Na 2 (MoO 4 )·2H 2 O: 20 g / L; ZrF 4 : 8g / L; H 2 C 2 o 4 : 0.2 wt%. Adjust the pH to 3, apply the passivation solution evenly on the rare earth-treated galvanized sheet, and cure at 100°C, curing time: natural cooling for 5 hours.
[0037] The prepared passivation film was tested for corrosion performance.
PUM
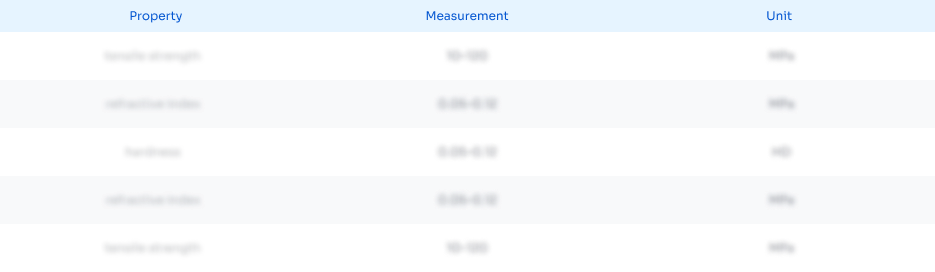
Abstract
Description
Claims
Application Information

- R&D
- Intellectual Property
- Life Sciences
- Materials
- Tech Scout
- Unparalleled Data Quality
- Higher Quality Content
- 60% Fewer Hallucinations
Browse by: Latest US Patents, China's latest patents, Technical Efficacy Thesaurus, Application Domain, Technology Topic, Popular Technical Reports.
© 2025 PatSnap. All rights reserved.Legal|Privacy policy|Modern Slavery Act Transparency Statement|Sitemap|About US| Contact US: help@patsnap.com