Production method for tripotassium phosphate
A technology of tripotassium phosphate and production method, applied in chemical instruments and methods, phosphorus compounds, inorganic chemistry, etc., can solve the problems of high cost of potassium phosphate products, long process flow, large pollution, etc., and achieve significant environmental protection value and raw material acquisition. Simple, low production cost effect
- Summary
- Abstract
- Description
- Claims
- Application Information
AI Technical Summary
Problems solved by technology
Method used
Image
Examples
Embodiment 1
[0048] A production method of tripotassium phosphate, specifically comprising the following steps:
[0049] (1) Preparation of urea phosphate solution: place urea phosphate in a dissolving tank, add water in a ratio of 1:1 according to the mass ratio of urea phosphate and water, and stir and dissolve according to a stirring speed of 30r / min, and heat up to After the temperature is 38°C, continue to stir and dissolve evenly to obtain a urea phosphate solution for use;
[0050] (2) adding potassium hydroxide to synthesize: the urea phosphate solution obtained in step 1) is transferred to the synthesis tank, and according to the mol ratio of urea phosphate and potassium hydroxide, the mol ratio is 1:2.95, adding potassium hydroxide solid, and Control the temperature during the reaction process to maintain at 40°C, and stir the reaction at a constant speed of 30r / min for 30 minutes to obtain the product slurry of tripotassium phosphate;
[0051] (3) Cooling crystallization and ce...
Embodiment 2
[0054] A production method of tripotassium phosphate, specifically comprising the following steps:
[0055] (1) Preparation of urea phosphate solution: place urea phosphate in a dissolving tank, add water in a ratio of 1:1 according to the mass ratio of urea phosphate and water, and stir and dissolve according to a stirring speed of 31r / min, and heat up to After the temperature is 38°C, continue to stir and dissolve evenly to obtain a urea phosphate solution for use;
[0056] (2) adding potassium hydroxide to synthesize: the urea phosphate solution obtained by step 1) is transferred in the synthesis tank, and according to the mol ratio of urea phosphate and potassium hydroxide, the mol ratio is 1:2.96, adding potassium hydroxide solution, and Control the temperature during the reaction process to maintain at 44°C, and stir the reaction at a constant speed of 30r / min for 36 minutes to obtain the product slurry of tripotassium phosphate;
[0057] (3) Cooling crystallization and...
Embodiment 3
[0060] A production method of tripotassium phosphate, specifically comprising the following steps:
[0061] (1) Preparation of Potassium Hydroxide Solution: Put Potassium Hydroxide solid in the dissolving tank, add water according to the mass ratio of Potassium Hydroxide and Water as 1:1, and stir and dissolve according to the stirring speed of 32r / min , and after heating up to a temperature of 38°C, continue to stir and dissolve evenly, and obtain a potassium hydroxide solution for use;
[0062] (2) add urea phosphate solid synthesis: the potassium hydroxide solution that step 1) obtains is transferred in the synthesis tank, and according to the mol ratio of urea phosphate and the mol ratio of potassium hydroxide is 1:3.05, add urea phosphate solid, and Control the temperature during the reaction process to maintain at 48°C, and stir the reaction at a constant speed of 30r / min for 42 minutes to obtain the product slurry of tripotassium phosphate;
[0063] (3) Cooling crystal...
PUM
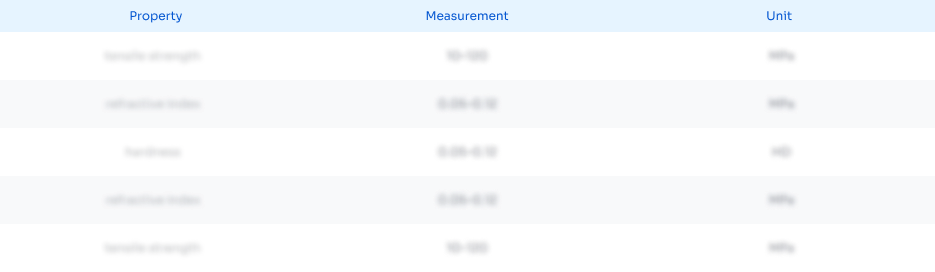
Abstract
Description
Claims
Application Information

- R&D
- Intellectual Property
- Life Sciences
- Materials
- Tech Scout
- Unparalleled Data Quality
- Higher Quality Content
- 60% Fewer Hallucinations
Browse by: Latest US Patents, China's latest patents, Technical Efficacy Thesaurus, Application Domain, Technology Topic, Popular Technical Reports.
© 2025 PatSnap. All rights reserved.Legal|Privacy policy|Modern Slavery Act Transparency Statement|Sitemap|About US| Contact US: help@patsnap.com