Regenerated MC nylon composite material and preparation method thereof
A technology of nylon composite material and nylon resin, which is applied in the field of polymer composite material preparation to achieve the effects of ensuring normal production, improving wear resistance, and convenient production
- Summary
- Abstract
- Description
- Claims
- Application Information
AI Technical Summary
Problems solved by technology
Method used
Image
Examples
Embodiment 1
[0032] After drying 57.5kg, MC regenerated nylon resin (relative viscosity 2.8, moisture content 1‰), 0.2kg antioxidant 1098, 0.2kg antioxidant 168, 8kgPOE-g-MAH, 0.6kg silicone, 1.5kg nylon Add carbon black masterbatch and 7kg molybdenum disulfide as the carrier to the high-speed mixer, stir well and then add to the main feeder of the twin-screw extruder, and add 25kg of glass fiber to the side feeder of the twin-screw extruder In the device, it is granulated by a twin-screw extruder, the speed of the host is 600r / min, the feeding temperature is 240-280°C, and the vacuum pressure is controlled at 0.06-0.08Mpa.
Embodiment 2
[0034] Dry 56.6kg of regenerated MC nylon resin (relative viscosity 2.6, moisture content 1‰), 0.2kg of antioxidant 1010, 0.2kg of antioxidant 168, 6kg of EPDM-g-MAH, 0.5kg of oxidized polyethylene wax, 1.5kg of Nylon as the carrier of nigrosine masterbatch and 10kg of ultra-high molecular weight polyethylene are added to the high-speed mixer, and after stirring evenly, they are added to the main feeder of the twin-screw extruder, and 25kg of glass fiber is added to the main feeder of the twin-screw extruder. In the side feeder, it is granulated by a twin-screw extruder, the speed of the main machine is 600r / min, the feeding temperature is 240-280°C, and the vacuum pressure is controlled at 0.06-0.08MPa.
Embodiment 3
[0036] 55.3kg dried regenerated MC nylon resin (relative viscosity 2.4, moisture content 1‰), 0.2kg antioxidant 1098, 0.2kg antioxidant 168, 5kgSEBS-g-MAH, 0.8kg ethylene bisstearamide, 1.5 Add kg Wuwei carrier carbon black masterbatch, 12kg polytetrafluoroethylene into the high-speed mixer, stir evenly and add to the main feeder of the twin-screw extruder, add 25kg of glass fiber to the side feeder of the twin-screw extruder In the feeder, it is granulated by a twin-screw extruder, the speed of the main machine is 600r / min, the feeding temperature is 240-280°C, and the vacuum pressure is controlled at 0.06-0.08MPa.
PUM
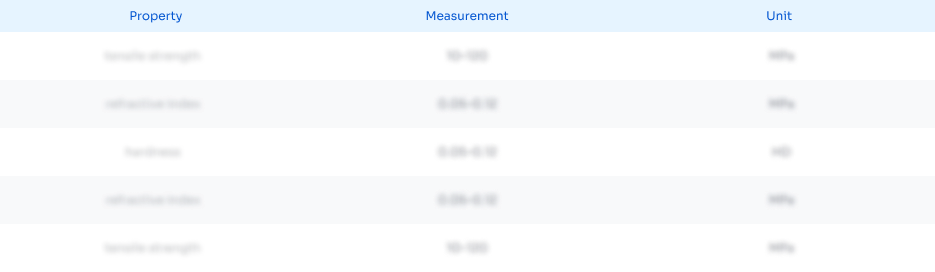
Abstract
Description
Claims
Application Information

- R&D
- Intellectual Property
- Life Sciences
- Materials
- Tech Scout
- Unparalleled Data Quality
- Higher Quality Content
- 60% Fewer Hallucinations
Browse by: Latest US Patents, China's latest patents, Technical Efficacy Thesaurus, Application Domain, Technology Topic, Popular Technical Reports.
© 2025 PatSnap. All rights reserved.Legal|Privacy policy|Modern Slavery Act Transparency Statement|Sitemap|About US| Contact US: help@patsnap.com