Ni-based high-temperature alloy surface boronizing agent and use method thereof
A technology of superalloy and boronizing agent, applied in metal material coating process, coating, solid diffusion coating and other directions, can solve the problems of thin infiltration layer, easy to fall off, etc., to achieve large infiltration layer depth, firm infiltration layer, Clean up easy effects
- Summary
- Abstract
- Description
- Claims
- Application Information
AI Technical Summary
Problems solved by technology
Method used
Image
Examples
Embodiment 1
[0024] The boronizing agent is composed of amorphous boron powder, activator and filler; among them, the activator is sodium fluoroaluminate and cerium oxide; the filler is silicon carbide. Each of the above-mentioned substances is a powder, and the above-mentioned respective powder substances are uniformly mixed.
[0025] The boronizing agent is calculated by weight percentage, 5% of 95% (mass) amorphous boron powder (molecular formula B), 5% sodium fluoroaluminate (molecular formula Na3SiF, Na3AlF6), 2% cerium oxide (molecular formula Ce 2 o 3 ) and 88% silicon carbide (molecular formula SiC).
[0026] Boronizing treatment on the surface of alloy GH4169 using the above boronizing agent: (see figure 2 )
[0027] The boronized surface of the superalloy sample is processed to a roughness of 3.2 in a conventional manner (such as surface polishing and deburring of the workpiece with a fluid viscoelastic material (composed of polymer carriers and abrasives)), and then Wash wi...
Embodiment 2
[0033] The boronizing agent is composed of amorphous boron powder, activator and filler; among them, the activator is sodium fluoroaluminate and cerium oxide; the filler is silicon carbide. Each of the above-mentioned substances is a powder, and the above-mentioned respective powder substances are uniformly mixed.
[0034] The boronizing agent is calculated by weight percentage, 6% of 95% (mass) amorphous boron powder (molecular formula B), 6% sodium fluoroaluminate (molecular formula Na3SiF, Na3AlF6), 3% cerium oxide (molecular formula Ce 2 o 3 ) and 85% silicon carbide (molecular formula SiC).
[0035] Boronizing treatment on the surface of alloy GH4169 using the above boronizing agent: (see figure 2 )
[0036] The boronized surface of the superalloy sample is processed to a roughness of 3.2 in a conventional manner (such as surface polishing and deburring of the workpiece with a fluid viscoelastic material (composed of polymer carriers and abrasives)), and then Wash wi...
PUM
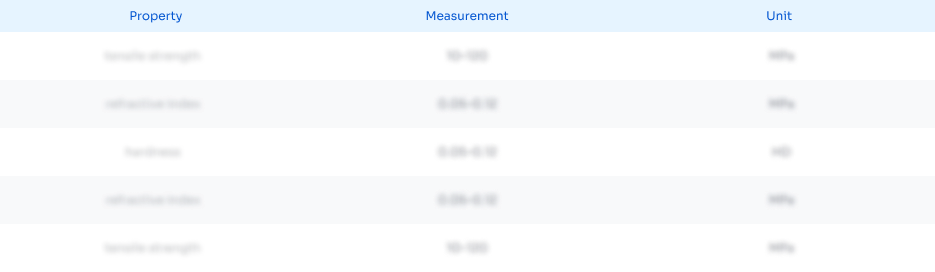
Abstract
Description
Claims
Application Information

- R&D
- Intellectual Property
- Life Sciences
- Materials
- Tech Scout
- Unparalleled Data Quality
- Higher Quality Content
- 60% Fewer Hallucinations
Browse by: Latest US Patents, China's latest patents, Technical Efficacy Thesaurus, Application Domain, Technology Topic, Popular Technical Reports.
© 2025 PatSnap. All rights reserved.Legal|Privacy policy|Modern Slavery Act Transparency Statement|Sitemap|About US| Contact US: help@patsnap.com