A kind of polylactic acid/abs alloy material and preparation method thereof
An alloy material and polylactic acid technology are applied in the field of polylactic acid/ABS alloy material and its preparation, green-based high-performance polylactic acid/ABS alloy material and its preparation field, which can solve the problem that the mechanical properties of the material have not been greatly improved and the preparation Due to the large size of the material phase region and the lack of compatibility, the effects of improved impact resistance, good biodegradability, high hardness and high strength are achieved.
- Summary
- Abstract
- Description
- Claims
- Application Information
AI Technical Summary
Problems solved by technology
Method used
Image
Examples
Embodiment 1~8
[0049] After PLA-1, ABS-1, ABS-2, ABS-3, ABS-4 and the third component (MMA-GMA-g-(PMMA)) were dried in a vacuum oven at 80°C for 24 hours, different grades were used ABS was melt-blended with PLA-1 and the third component respectively according to the composition ratio in Table 1; the three raw materials were mixed and stirred at room temperature and then added to the internal mixer. The temperature of the internal mixer was 190°C, and the screw speed was set at 50rpm. , Discharge after banburying for 10 minutes.
[0050] The above mixed samples were hot-pressed into a sheet with a thickness of 0.5mm in a hot press at 200°C, and a standard test sample was prepared with a standard dumbbell-shaped punching knife for performance testing. The results are shown in Table 1.
Embodiment 9
[0061] After PLA-2, ABS-3 and the third component (MMA-GMA-g-(PMMA)) were dried in a vacuum oven at 80°C for 24 hours, 50 g of PLA-2, 50 g of ABS-3 and 3 g The third component (MMA-GMA-g-(PMMA)) was mixed and added to the internal mixer. The temperature of the internal mixer was 190° C., the screw speed was set at 50 rpm, and the material was discharged after internal mixing for 10 minutes.
[0062] The above mixed samples were hot pressed into a sheet with a thickness of 0.5mm in a hot press at 200°C, and a standard test sample was prepared with a standard dumbbell-shaped punching knife for performance testing.
Embodiment 10
[0064] After PLA-1, PLA-2, ABS-3 and the third component (MMA-GMA-g-(PMMA)) were dried in a vacuum oven at 80°C for 24 hours, 25 grams of PLA-1, 25 grams of PLA- 2. 50 grams of ABS-3 and 3 grams of the third component (MMA-GMA-g-(PMMA)) are mixed and added to the internal mixer. The temperature of the internal mixer is 190°C, the screw speed is set at 50rpm, and the internal mixer is mixed for 10 Discharge in minutes.
[0065] The above mixed samples were hot pressed into a sheet with a thickness of 0.5mm in a hot press at 200°C, and a standard test sample was prepared with a standard dumbbell-shaped punching knife for performance testing.
PUM
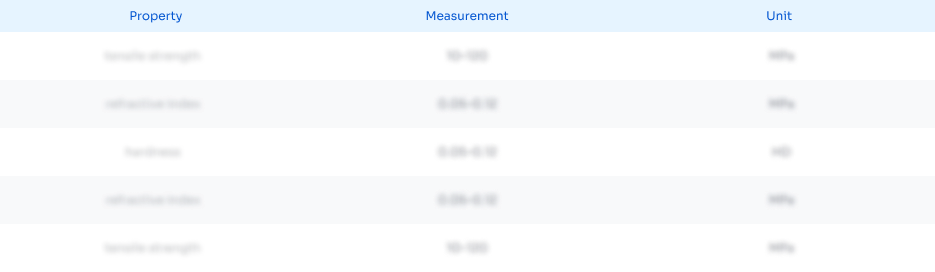
Abstract
Description
Claims
Application Information

- R&D
- Intellectual Property
- Life Sciences
- Materials
- Tech Scout
- Unparalleled Data Quality
- Higher Quality Content
- 60% Fewer Hallucinations
Browse by: Latest US Patents, China's latest patents, Technical Efficacy Thesaurus, Application Domain, Technology Topic, Popular Technical Reports.
© 2025 PatSnap. All rights reserved.Legal|Privacy policy|Modern Slavery Act Transparency Statement|Sitemap|About US| Contact US: help@patsnap.com