A kind of preparation method of epoxy polyamide papermaking wet strength agent
A technology of epoxy polyamide and wet strength agent, applied in the direction of adding reinforcing agent, etc., can solve the problems of poor product quality controllability, poor product quality controllability, dark product color, etc., to reduce molecular branching reaction, Improved controllability and stability, improved wet strength effects
- Summary
- Abstract
- Description
- Claims
- Application Information
AI Technical Summary
Problems solved by technology
Method used
Image
Examples
Embodiment 1
[0018] 1) Synthesis of polyamide intermediate: Stir and mix 103 grams of diethylenetriamine and 202 grams of diethyl adipate, raise the temperature to 120°C, keep the temperature for 4 hours and then cool down, then add 208 grams of deionized water to obtain a polyamide intermediate body water solution.
[0019] 2) Add 600 grams of early stage water to the above polyamide intermediate aqueous solution, stir evenly, slowly add 105 grams of epichlorohydrin dropwise within 30 minutes, stir for 30 minutes, heat up to 30°C, and keep warm for 5 hours; then heat up to 45°C, Keep warm for 4 hours; finally add 20 grams of 1% hydrochloric acid to terminate the reaction, add 250 grams of late water after cooling down, and the resulting product is epoxy polyamide paper-making wet strength agent with a shear viscosity of 30 centipoise.
Embodiment 2
[0021] 1) Synthesis of polyamide intermediate: Stir and mix 146 grams of triethylenetetramine and 174 grams of dimethyl adipate, raise the temperature to 90°C, keep the temperature for 10 hours, then cool down, then add 246 grams of deionized water to obtain a polyamide intermediate body water solution.
[0022] 2) Add 450 grams of early stage water to the above polyamide intermediate aqueous solution, stir evenly, slowly add 135 grams of epichlorohydrin dropwise within 60 minutes, stir for 30 minutes, heat up to 45°C, and keep warm for 1 hour; then heat up to 85°C , keep warm for 0.5 hour; finally add 5 grams of 25% sulfuric acid to terminate the reaction, add 300 grams of later stage water after cooling down, the resulting product is epoxy polyamide papermaking wet strength agent, and the shear viscosity is 25 centipoise.
Embodiment 3
[0024] 1) Synthesis of polyamide intermediates: Stir and mix 116 grams of hexamethylenediamine and 194 grams of dimethyl terephthalate, heat up to 160°C, keep warm for 2 hours, then cool down, then add 275 grams of deionized water to obtain polyamide intermediates body water solution.
[0025] 2) Add 530 grams of early stage water to the above-mentioned polyamide intermediate aqueous solution, stir evenly, slowly add 90 grams of epichlorohydrin dropwise within 45 minutes, stir for 30 minutes, heat up to 35°C, and keep warm for 3 hours; then heat up to 65°C ℃, keep warm for 2 hours; finally add 15 grams of 10% nitric acid to terminate the reaction, add 160 grams of late water after cooling down, and the resulting product is an epoxy polyamide papermaking wet strength agent with a shear viscosity of 35 centipoise.
PUM
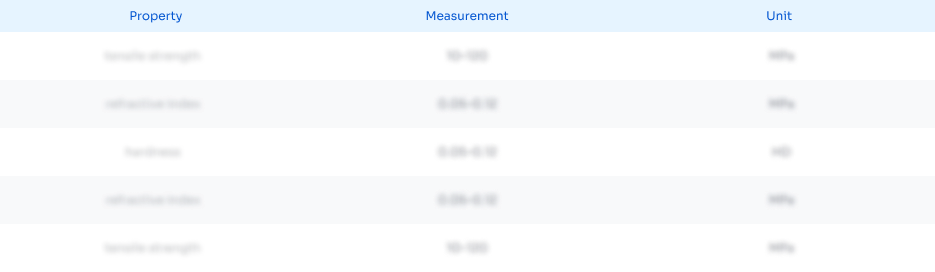
Abstract
Description
Claims
Application Information

- R&D Engineer
- R&D Manager
- IP Professional
- Industry Leading Data Capabilities
- Powerful AI technology
- Patent DNA Extraction
Browse by: Latest US Patents, China's latest patents, Technical Efficacy Thesaurus, Application Domain, Technology Topic, Popular Technical Reports.
© 2024 PatSnap. All rights reserved.Legal|Privacy policy|Modern Slavery Act Transparency Statement|Sitemap|About US| Contact US: help@patsnap.com