Two-motor driving type cascading multi-level inverter system without active front end and control method thereof
A cascaded multi-level, motor-driven technology, applied in motor generator control, motor/generator/inverter limiter, control system, etc., can solve the adverse effects of increasing the complexity of the control system and system reliability , increase the cost of detection links, etc., to achieve the effect of improving energy utilization efficiency, obvious energy saving effect, avoiding energy feeding and harmonic injection
- Summary
- Abstract
- Description
- Claims
- Application Information
AI Technical Summary
Problems solved by technology
Method used
Image
Examples
Embodiment Construction
[0030] In order to make the technical solutions and beneficial effects of the present invention more obvious and understandable, the present invention will be further described in detail below in conjunction with the accompanying drawings and specific implementation methods. Wherein, it is assumed that the motor M1 works in a braking state, and the motor M2 works in a motoring state.
[0031] image 3 For the present invention, two motors drive the cascaded multi-level inverter system, in figure 1 The energy feedback coupling unit is added to the traditional cascaded multilevel inverter shown. See figure 1 , the traditional cascaded multilevel inverter consists of 3n cascaded power units based on three-phase uncontrolled rectifier circuits and H-bridge inverter circuits. The circuit structure of the power units is shown in figure 2 , n power units are cascaded as one phase of the three-phase inverter.
[0032] Figure 4 It is a schematic diagram of the circuit structure ...
PUM
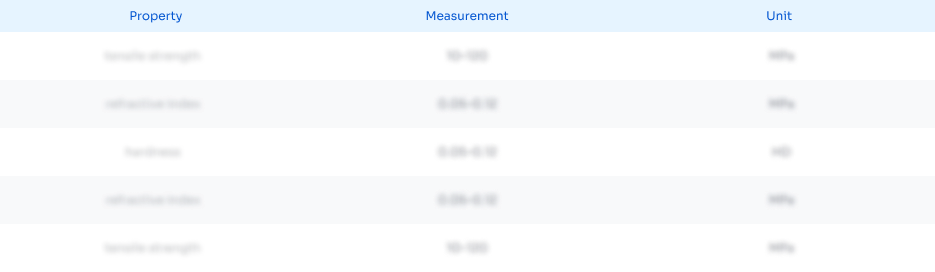
Abstract
Description
Claims
Application Information

- R&D
- Intellectual Property
- Life Sciences
- Materials
- Tech Scout
- Unparalleled Data Quality
- Higher Quality Content
- 60% Fewer Hallucinations
Browse by: Latest US Patents, China's latest patents, Technical Efficacy Thesaurus, Application Domain, Technology Topic, Popular Technical Reports.
© 2025 PatSnap. All rights reserved.Legal|Privacy policy|Modern Slavery Act Transparency Statement|Sitemap|About US| Contact US: help@patsnap.com