Monocrystalline silicon wafer texturing additive, texturing solution and corresponding texturing method
A technology of monocrystalline silicon wafers and additives, applied in chemical instruments and methods, crystal growth, after treatment, etc., can solve problems such as enlarged pyramid size, low solar cell efficiency, and weakened corrosion rate, and achieve improved stability and consistency Sexuality, cost reduction, and the effect of reducing usage
- Summary
- Abstract
- Description
- Claims
- Application Information
AI Technical Summary
Problems solved by technology
Method used
Image
Examples
Embodiment Construction
[0026] specific implementation plan
[0027] The purpose and effects of the present invention will be described in detail below in conjunction with specific embodiments and accompanying drawings.
[0028] Monocrystalline silicon wafer texturing additive of the present invention comprises terpineol (C 10 h 18 O), polyethylene glycol ether (), lactic acid (C 3 h 6 o 3 ), sodium acetate (CH 3 COONa) and alkali, the mass percent concentration of described terpineol, polyethylene glycol ether, lactic acid, sodium acetate, alkali is respectively 0.1-3%, 0.3-5%, 0.01-5%, 0.01-5% and 0.1% -2%. The alkali is sodium hydroxide (NaOH) or potassium hydroxide (NaOH) or the like.
[0029] In the first embodiment of the monocrystalline silicon wafer texturing additive of the present invention, the mass percentage concentrations of the terpineol, polyethylene glycol ether, lactic acid, sodium acetate, and sodium hydroxide are respectively 0.5%, 0.3%, 0.05%, 0.1%, and 2.0%.
[0030] In...
PUM
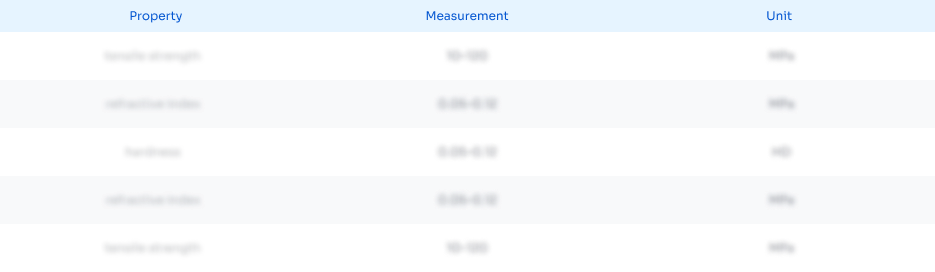
Abstract
Description
Claims
Application Information

- Generate Ideas
- Intellectual Property
- Life Sciences
- Materials
- Tech Scout
- Unparalleled Data Quality
- Higher Quality Content
- 60% Fewer Hallucinations
Browse by: Latest US Patents, China's latest patents, Technical Efficacy Thesaurus, Application Domain, Technology Topic, Popular Technical Reports.
© 2025 PatSnap. All rights reserved.Legal|Privacy policy|Modern Slavery Act Transparency Statement|Sitemap|About US| Contact US: help@patsnap.com