Dyeing Technology of Cotton Knitted Fabric
A cotton knitted fabric and process technology, applied in the field of cotton knitted fabric dyeing process, can solve the problems of low probability of one-time dyeing success, large waste of cooling water, high coal consumption, etc., to improve the probability of one-time dyeing success, reduce The effect of electricity consumption and capital cost reduction
- Summary
- Abstract
- Description
- Claims
- Application Information
AI Technical Summary
Problems solved by technology
Method used
Image
Examples
Embodiment 1
[0035] The dyeing process of this embodiment is all suitable for light, medium and dark dyes.
[0036] The technological process of the present embodiment is as follows:
[0037] 1. At room temperature, add water to the dyeing machine. It takes 3 minutes to add water. The amount of water added is controlled according to the amount of pre-treated cotton knitted fabric in the dyeing machine and the predetermined bath ratio;
[0038] 2. Raise the temperature to the first set temperature of 35°C, and maintain the temperature, add the dyeing accelerator sodium sulfate, the first soda ash and leveling agent to the dyeing machine, add the dyeing accelerator, the first soda ash and leveling agent The time of using the agent is 3 minutes, and the dyeing machine runs for 15 minutes after adding;
[0039] 3. Add the reactive dyes to the dyeing machine after using clear water as the chemical material. It takes 10 minutes to add the melted reactive dyes to the dyeing machine, and then the...
Embodiment 2
[0056] The dyeing process of the present embodiment is all suitable for reactive dyes such as reactive bright yellow, reactive fruit green and reactive emerald blue.
[0057] 1. At room temperature, add water to the dyeing machine. It takes 5 minutes to add water. The amount of water added is controlled according to the amount of pre-treated cotton knitted fabric in the dyeing machine and the predetermined bath ratio;
[0058] 2. Raise the temperature to the first set temperature of 40°C, and maintain the temperature, add the dyeing accelerator salt, the first substitute alkali and leveling agent into the dyeing machine, add the dyeing accelerator, the first substitute alkali and leveling agent The time of using the agent is 5 minutes, and the dyeing machine runs for 20 minutes after adding;
[0059] 3. Add the reactive dye to the dyeing machine after using clear water as the chemical material. The time to add the melted reactive dye to the dyeing machine is 25 minutes, and th...
PUM
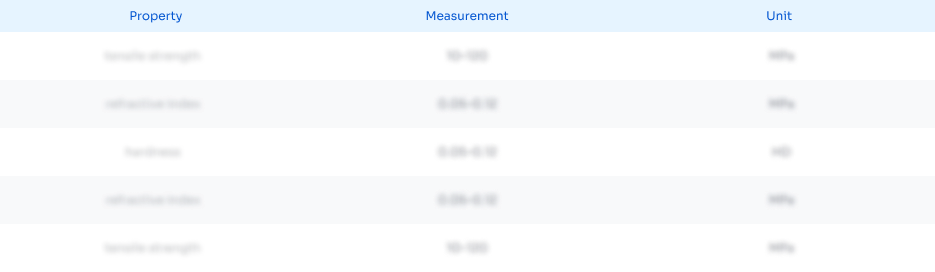
Abstract
Description
Claims
Application Information

- R&D
- Intellectual Property
- Life Sciences
- Materials
- Tech Scout
- Unparalleled Data Quality
- Higher Quality Content
- 60% Fewer Hallucinations
Browse by: Latest US Patents, China's latest patents, Technical Efficacy Thesaurus, Application Domain, Technology Topic, Popular Technical Reports.
© 2025 PatSnap. All rights reserved.Legal|Privacy policy|Modern Slavery Act Transparency Statement|Sitemap|About US| Contact US: help@patsnap.com