Austenite stainless steel and production method thereof
A technology of austenitic stainless steel and production method, which is applied in the field of stainless steel processing, can solve the problems of low first-grade product rate, impact on service performance, and recessed defective shells, etc., so as to reduce the occurrence of thermally processed surface and edge cracks, reduce The generation of cracks inside and on the surface of the slab, and the effect of improving product quality
- Summary
- Abstract
- Description
- Claims
- Application Information
AI Technical Summary
Problems solved by technology
Method used
Image
Examples
Embodiment 1
[0040] A kind of austenitic stainless steel, its chemical composition weight percent ratio is: 0.018%, Si: 0.55%, Mn: 1.35%, Cr: 16.7%, Ni: 10.05%, Mo: 2.05%, N: 0.020%, P: 0.035%, S: 0.002%, [S1] B: 30ppm, the rest is Fe and unavoidable impurity elements; its DG=3.49*(Cr+Mo+1.5*Si) -2.5*(Ni+30*C The value of +30*N+0.5*Mn+0.3*Cu)-30.65 is 7.90, and the value of Md30 is -45.6.
[0041] A production method of austenitic stainless steel, comprising the steps of:
[0042] (1) Prepare a slab that meets the above composition requirements, with a DG value of 7.9;
[0043] (2) AOD, LF enhanced deoxidation and desulphurization, total O: 40ppm, S: 20ppm;
[0044] (3) Add a certain amount of Fe-B before LF tapping, and the B content is 30ppm;
[0045] (3) LF ensures good cleanliness of molten steel, soft blowing and sedation time of 12 minutes;
[0046] (4) The continuous casting superheat is 30°C, the constant casting speed is 1.10m / min, and the secondary cooling water is reduced by...
Embodiment 2
[0052] An austenitic stainless steel, the weight percentage of chemical composition is: C=0.016%, Si: 0.4%, Mn: 1.0%, Cr: 16.5%%, Ni: 10.0%, N: 0.050%, Mo: 2.50%, P =0.0350%, S=0.0025%, B: 20ppm, the rest is Fe and unavoidable impurity elements; DG=6.02, Md30=-35.7.
[0053] A production method of austenitic stainless steel, comprising the steps of:
[0054] (1) Prepare a slab that meets the above composition requirements, and the DG value is between 6.02;
[0055] (2) AOD, LF enhanced deoxidation and desulphurization, total O: 45ppm, S: 15ppm;
[0056] (3) Add a certain amount of Fe-B before tapping LF;
[0057] (3) LF ensures good cleanliness of molten steel, soft blowing and sedation time of 15 minutes;
[0058] (4) The superheat of continuous casting is 20℃, the constant tension is 1.15m / min, and the secondary cooling water is weakly cooled;
[0059] (5) Hot rolling, the heating temperature in the heating furnace is 1300°C, and the furnace temperature is 1230°C; after he...
Embodiment 3
[0064] A kind of austenitic stainless steel, the weight percent of chemical composition is: C=0.015%, Si: 0.6%, Mn: 1.5%, Cr: 18.0%, Ni: 11.0%, N: 0.010%, Mo: 2.00%, P= 0.030%, S≤0.002%, B: 40ppm, the rest is Fe and unavoidable impurity elements; DG=8.30, Md30=-50.
[0065] A production method of austenitic stainless steel, comprising the steps of:
[0066] (1) Prepare a slab meeting the above composition requirements, with a DG value of 8.30;
[0067] (2) AOD, LF enhanced deoxidation and desulphurization, total O: 40ppm, S: 20ppm;
[0068] (3) Add a certain amount of Fe-B before tapping LF;
[0069] (3) LF ensures good cleanliness of molten steel, soft blowing and sedation time of 11 minutes;
[0070] (4) The continuous casting superheat is 40°C, the constant casting speed is 1.1m / min, and the secondary cooling water is weakly cooled;
[0071] (5) Hot rolling, the heating temperature in the heating furnace is 1250°C, and the furnace temperature is 1210°C. After heat defo...
PUM
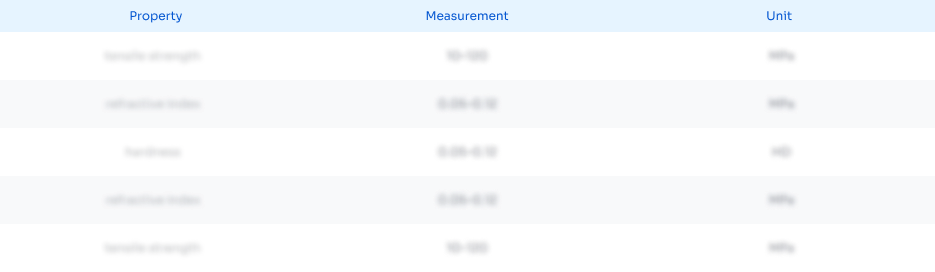
Abstract
Description
Claims
Application Information

- Generate Ideas
- Intellectual Property
- Life Sciences
- Materials
- Tech Scout
- Unparalleled Data Quality
- Higher Quality Content
- 60% Fewer Hallucinations
Browse by: Latest US Patents, China's latest patents, Technical Efficacy Thesaurus, Application Domain, Technology Topic, Popular Technical Reports.
© 2025 PatSnap. All rights reserved.Legal|Privacy policy|Modern Slavery Act Transparency Statement|Sitemap|About US| Contact US: help@patsnap.com