Anti-static EVA material and preparation method thereof
An anti-static, EVA26%VA65 technology, applied in the field of anti-static materials, can solve the problems of high cost, short service life, and inability to permanently anti-static, and achieve high stability, long service life, and not easy to age.
- Summary
- Abstract
- Description
- Claims
- Application Information
AI Technical Summary
Problems solved by technology
Method used
Examples
Embodiment 1
[0031] Embodiment 1: the raw material of following parts by weight is carried out banburying:
[0032] EVA 26%VA 60 parts
[0033] EPDM 5725 10 copies
[0035] 1 part white oil
[0036] Foaming agent 1 part
[0037] 0.2 parts of coupling agent
[0038] Zinc oxide powder 0.5 parts
[0039] 0.5 parts of stearic acid
[0040] Then add 5 parts of conductive carbon black N990 to continue banburying. During banburying, keep the temperature at 110°C and air pressure of 0.7kg, and banbury for 10 minutes; at a temperature of 80°C, open the mixture to 15mm once, 1mm once; After smelting, granulate, the granulation temperature is 80°C, and the cooling water must be kept smooth; finally, the obtained granules are sent to the foaming machine for foaming, and the temperature of the foaming machine is controlled at 165°C for 10 minutes and the pressure is 170kg. After the material is parked for 6 hours, it will be tested.
Embodiment 2
[0041] Embodiment 2: the raw material of following parts by weight is carried out banburying:
[0042] EVA 26%VA 70 parts
[0043] EPDM 5725 20 copies
[0044] Talcum powder 15 parts
[0045] White oil 5 parts
[0046] Foaming agent 5 parts
[0047] 0.6 parts of coupling agent
[0048] Zinc oxide powder 1.5 parts
[0049] 1.5 parts of stearic acid
[0050] Then add 15 parts of conductive carbon black N990 to continue banburying. During the banburying, the temperature was kept at 110°C, and the air pressure was 0.8kg, and banburying was carried out for 10 minutes; After smelting, granulate, the granulation temperature is 85°C, and the cooling water must be kept smooth; finally, the obtained granules are sent to the foaming machine for foaming, and the temperature of the foaming machine is controlled at 165°C for 10 minutes and the pressure is 170kg. After the material is parked for 6 hours, it will be tested.
Embodiment 3
[0051] Embodiment 3: the raw material of following parts by weight is carried out banburying:
[0052] EVA 26%VA 65 parts
[0053] EPDM 5725 15 copies
[0054] Talc powder 10 parts
[0055] 3 parts white oil
[0056] Foaming agent 3 parts
[0057] 0.4 parts of coupling agent
[0058] Zinc oxide powder 1 part
[0059] 1 part stearic acid
[0060] Then add 10 parts of conductive carbon black N990 to continue banburying. During the banburying, the temperature is kept at 110°C and the air pressure is 0.8kg, and banburying is carried out for 10 minutes; After smelting, granulate, the granulation temperature is 85°C, and the cooling water must be kept smooth; finally, the obtained granules are sent to the foaming machine for foaming, and the temperature of the foaming machine is controlled at 165°C for 10 minutes and the pressure is 170kg. After the material is parked for 6 hours, it will be tested.
[0061] The performance of the conductive shoe sole material of the present...
PUM
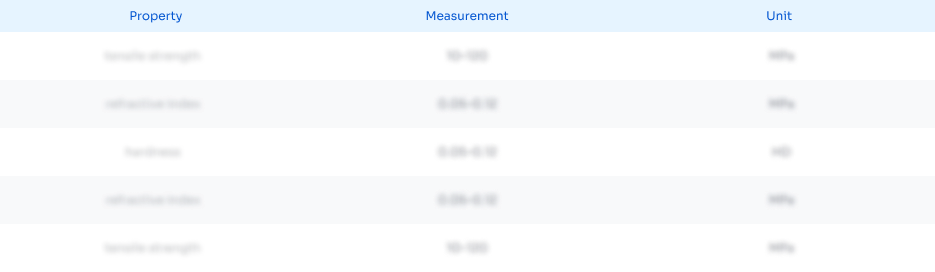
Abstract
Description
Claims
Application Information

- R&D Engineer
- R&D Manager
- IP Professional
- Industry Leading Data Capabilities
- Powerful AI technology
- Patent DNA Extraction
Browse by: Latest US Patents, China's latest patents, Technical Efficacy Thesaurus, Application Domain, Technology Topic, Popular Technical Reports.
© 2024 PatSnap. All rights reserved.Legal|Privacy policy|Modern Slavery Act Transparency Statement|Sitemap|About US| Contact US: help@patsnap.com