Process for simultaneously desulfurizing and denitrifying to coproduce calcium sulfate whisker
A calcium sulfate whisker, desulfurization and denitrification technology, applied in crystal growth, single crystal growth, single crystal growth, etc., can solve the problems of high operating costs, low value of by-products, low system investment, resource and energy consumption, etc.
- Summary
- Abstract
- Description
- Claims
- Application Information
AI Technical Summary
Problems solved by technology
Method used
Image
Examples
Embodiment 1
[0035] figure 1 Medium desulfurization and denitrification absorption tower 1, slurry tank 2, filter 3, filtrate tank 4, washing liquid tank 5, slurry pump 6, slurry pump 7, filtrate pump 8, washing liquid pump 9, tower electrolysis device 10; lime Powder A, flue gas B, purified flue gas C, washing process water D, gypsum whiskers E.
[0036] The flue gas B at a temperature of 110°C enters the middle part of the desulfurization and denitrification absorption tower 1, and is in countercurrent contact with the circulating slurry, feed slurry, filtrate and washing process water sprayed from the upper part. The circulation of the slurry in the tower is not shown in the figure. The slurry in the tower is output by the slurry pump 6, one part is sent to the slurry tank 2 to make slurry with the input lime powder A, and then sent to the desulfurization and denitrification absorption tower 1 by the slurry pump 7, and the other part is sent to the filter 3, and the filtrate is collecte...
Embodiment 2
[0040] figure 2 Medium desulfurization and denitrification absorption tower 1, slurry tank 2, filter 3, filtrate tank 4, washing liquid tank 5, slurry pump 6, slurry pump 7, filtrate pump 8, washing liquid pump 9, external electrolysis device 10; lime Powder A, flue gas B, purified flue gas C, washing process water D, gypsum whiskers E.
[0041] The flue gas B at a temperature of 110°C enters the middle part of the desulfurization and denitrification absorption tower 1, and is in countercurrent contact with the circulating slurry, feed slurry, filtrate and washing process water sprayed from the upper part. The circulation of the slurry in the tower is not shown in the figure. The slurry in the tower flows through the electrolysis device 10 outside the tower, one part flows into the feeding slurry tank 2 to make slurry with the input lime powder A, and then is sent to the desulfurization and denitrification absorption tower 1 by the slurry pump 7, and the other part is output ...
Embodiment 3
[0045] image 3 Medium desulfurization and denitrification absorption tower 1, filter 2, slurry tank 3, washing liquid tank 4, slurry pump 5, circulating slurry pump 6, slurry pump 7, washing liquid pump 8, tower electrolysis device 9; flue gas A, Purify flue gas B, wash process water C, lime powder D, gypsum whiskers E.
[0046] The flue gas A at a temperature of 110°C enters the middle part of the desulfurization and denitrification absorption tower 1, and is in countercurrent contact with the circulating slurry, feed slurry and washing process water sprayed from the upper part. Most of the slurry in the tower is circulated by the circulating slurry pump 6, and a small part The output of the slurry pump 5 is sent to the filter 2 for filtration, the filtrate and the input lime powder D are made into slurry in the slurry tank 3, and then sent to the desulfurization and denitrification absorption tower 1 by the slurry pump 7, and the filtered solid phase is washed with the wash...
PUM
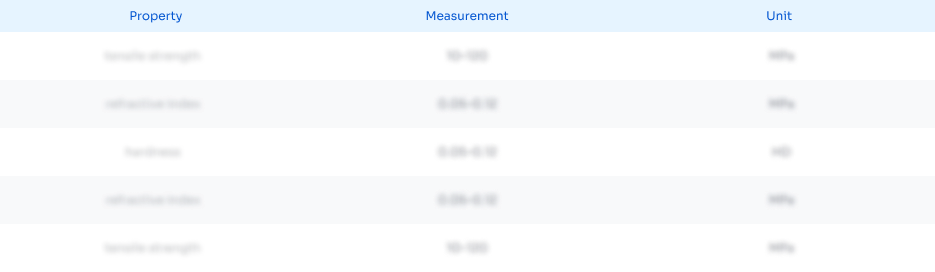
Abstract
Description
Claims
Application Information

- Generate Ideas
- Intellectual Property
- Life Sciences
- Materials
- Tech Scout
- Unparalleled Data Quality
- Higher Quality Content
- 60% Fewer Hallucinations
Browse by: Latest US Patents, China's latest patents, Technical Efficacy Thesaurus, Application Domain, Technology Topic, Popular Technical Reports.
© 2025 PatSnap. All rights reserved.Legal|Privacy policy|Modern Slavery Act Transparency Statement|Sitemap|About US| Contact US: help@patsnap.com