Method used for preparing methyl acetate
A technology of methyl acetate and dimethyl ether, which is applied in the field of new fixed-bed reactor technology, can solve the problems of difficult industrial production, uneven temperature distribution of the catalyst bed, and difficult control, so as to improve selectivity, avoid hot spots, Effect of prolonging catalyst life
- Summary
- Abstract
- Description
- Claims
- Application Information
AI Technical Summary
Problems solved by technology
Method used
Image
Examples
Embodiment 1
[0028] The preparation of embodiment 1 catalyst
[0029] Catalysts are expressed in n%M / MOR, where:
[0030] Heteroatoms: M = iron (Fe), gallium (Ga);
[0031] Loading metal: M = iron (Fe), copper (Cu), silver (Ag), rhodium (Rh), platinum (Pt), palladium (Pd), cobalt (Co), iridium (Ir);
[0032] n = the mass percentage of the metal in the total weight of the catalyst × 100; the metal in the supported catalyst is in an oxidation state, and the content is represented by elemental metal.
[0033] 1.1 Synthesis of sodium mordenite
[0034] Dissolve 19 grams of NaOH into 40 ml of deionized water, then add a certain amount of sodium aluminate or a mixture of sodium aluminate + iron nitrate or sodium aluminate + gallium oxide, and stir until completely dissolved. Add 650ml of water to the resulting solution for dilution, then add a certain amount of SiO 2powder and stirred for 30 minutes. The resulting material was placed in a Teflon-lined stainless steel reaction vessel. Cryst...
Embodiment 2
[0049] Embodiment 2. Catalyst pretreatment and reaction
[0050] At the beginning of the investigation, the catalyst was activated at 550°C in a nitrogen atmosphere for 4 hours, then the temperature of the bed was lowered to 300°C, and gaseous pyridine diluted with nitrogen was introduced for adsorption. After 1 hour of adsorption, purging of pure nitrogen was carried out for 30 minutes at the same temperature. A certain proportion of dimethyl ether, a mixture of carbon monoxide and hydrogen is introduced to increase the pressure and react. The reactor is heated by an electric furnace, and the reaction temperature is determined by a thermocouple inserted into the catalyst bed.
Embodiment 3
[0051] Embodiment 3. the analytical method of product
[0052] The starting materials and the resulting products were analyzed using an Agilent 7890A gas chromatograph. The chromatograph is equipped with dual detectors FID and TCD, and has a ten-way valve, which allows the products to enter the packed column and capillary column respectively at the same time. The hydrogen flame detector detects hydrocarbons, alcohols and ethers in the product, and the thermal conductivity detector detects carbon monoxide and hydrogen in the raw materials and products. Data were processed with Agilent's Chemstation software.
[0053] The specific chromatographic conditions of Agilent are as follows:
[0054] Chromatography: Agilent 7890A
[0055] FID column: HP-PLOT-Q 19091S-001, 50m x 0.2mm (inner diameter), 0.5μm
[0056] film thickness
[0057] Carrier gas: helium, 2.5ml / min
[0058] Oven temperature: 35°C for 5 minutes
[0059] 35-150°C, 5°C / min
[0060] 150℃ for...
PUM
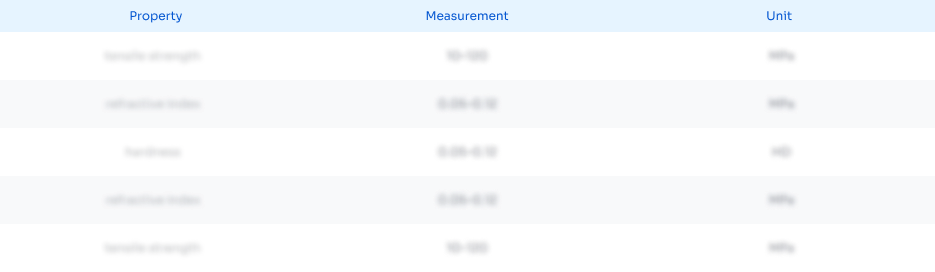
Abstract
Description
Claims
Application Information

- R&D
- Intellectual Property
- Life Sciences
- Materials
- Tech Scout
- Unparalleled Data Quality
- Higher Quality Content
- 60% Fewer Hallucinations
Browse by: Latest US Patents, China's latest patents, Technical Efficacy Thesaurus, Application Domain, Technology Topic, Popular Technical Reports.
© 2025 PatSnap. All rights reserved.Legal|Privacy policy|Modern Slavery Act Transparency Statement|Sitemap|About US| Contact US: help@patsnap.com