High-shear reaction kettle and application of kettle to production of suspension polymerization polyethylene
A polyethylene oxide and suspension polymerization technology, which is applied in the field of high-shear reactors in the field of chemical engineering technology, can solve the problems of density difference between particles and fluid medium, insufficient axial movement speed, dead angle of reactor, etc., and achieve product particle size The effect of uniform, accelerated axial movement speed and large radial shear force
- Summary
- Abstract
- Description
- Claims
- Application Information
AI Technical Summary
Problems solved by technology
Method used
Image
Examples
Embodiment 1
[0024] Such as figure 1 As shown, a high-shear reactor includes a motor drive device 1, a stirring device, a kettle body, a jacket 5, and a baffle 10. The motor drive device 1 is connected to the stirring device through a transmission device 2, and the motor drive device 1 Located on the top of the kettle body, a stirring device is arranged in the kettle body. The stirring device includes a stirring shaft 8 and a paddle 6 arranged on the stirring shaft 8, and the stirring shaft 8 is connected to a motor driving device. The ratio of the diameter of the blade d to the diameter D of the kettle body d / D=0.35, the ratio of the height h (vertical height) of the blade to the diameter d of the blade is 1.0, and the 45°blade turbine type is used to push downwards, and the corresponding blade end line The speed is 5D / d (m / s). The diameter d of the blade is smaller than the diameter D of the kettle body, which can provide a larger axial fluid rising space. The single-piece baffle design...
Embodiment 2
[0032] Step 1: Same as Example 1, except that the amount of each component of the catalyst is increased by 5 times in the same proportion, the other conditions remain unchanged.
[0033] Step 2: The reactor volume is 20m 3 , Except that the amount of solvent added is changed to 10m 3 Otherwise, the other conditions are the same as in Example 1.
[0034] After reacting for 20 hours, the suspended materials in the reactor are filtered by a filter and dried in a fluidized bed. The conversion rate of ethylene oxide reaches 99.1%, and a polyethylene oxide with a molecular weight of about 420,000 is obtained. The laser particle size analysis shows the average particle size of the product. It is about 47μm, and the sieving rate of 20-mesh sieve is 99%.
Embodiment 3
[0036] Step 1: Same as Example 2, except that the added amounts of calcium metal, propylene oxide, and acetonitrile are sequentially changed to 15 kg, 21.7 kg and 6.2 kg, and other conditions remain unchanged.
[0037] Step 2: Same as Example 2, except that the shear speed is changed to 300 rpm and the amount of 90# solvent added is changed to 8 m3, the other conditions remain unchanged.
[0038] After reacting for 12 hours, the suspended materials in the reactor are filtered by a filter and dried in a fluidized bed. The conversion rate of ethylene oxide reaches 97.8%, and a polyethylene oxide with a molecular weight of about 900,000 is obtained. The laser particle size analysis shows the average particle size of the product. It is about 115μm, and the sieving rate of 20-mesh sieve is 98%.
PUM
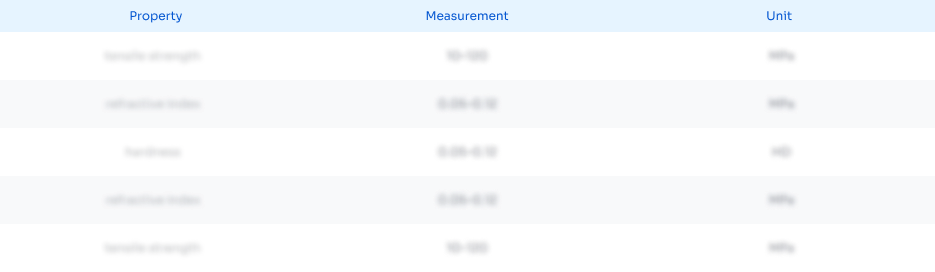
Abstract
Description
Claims
Application Information

- Generate Ideas
- Intellectual Property
- Life Sciences
- Materials
- Tech Scout
- Unparalleled Data Quality
- Higher Quality Content
- 60% Fewer Hallucinations
Browse by: Latest US Patents, China's latest patents, Technical Efficacy Thesaurus, Application Domain, Technology Topic, Popular Technical Reports.
© 2025 PatSnap. All rights reserved.Legal|Privacy policy|Modern Slavery Act Transparency Statement|Sitemap|About US| Contact US: help@patsnap.com