Preparation method of calcium ferrite
A technology of calcium ferrite and calcium sulfate, applied in the field of metallurgy, can solve the problems of low utilization value, waste of resources, etc., and achieve the effects of high added value, high conversion rate, and easy promotion.
- Summary
- Abstract
- Description
- Claims
- Application Information
AI Technical Summary
Problems solved by technology
Method used
Examples
preparation example Construction
[0034] The preparation method of calcium ferrite of the present invention is characterized in that: comprises the steps:
[0035] (a) Take gypsum, pyrite and iron supplement and mix them to obtain a mixed material;
[0036] Among them, calcium sulfate in gypsum: ferrous disulfide in pyrite: iron element in iron supplement = 1:0.1~2.5:0~2 in molar ratio, and calcium element in mixed material in molar ratio: iron element=1: 1-2.5, the moisture content of the gypsum is less than 10wt%, and the moisture content of the pyrite is 0.1-15wt%;
[0037] (b) Calcining the mixed material in a protective atmosphere, the roasting temperature is 900-1500°C, the roasting time is 0.1-4h, after the roasting is completed, cool down to obtain calcium ferrite;
[0038] Wherein, the protective atmosphere is an inert atmosphere, a reducing atmosphere or an oxidizing atmosphere with an oxygen content of less than 5wt%.
[0039] The iron supplement mentioned in the present invention is a substance c...
Embodiment 1
[0052] The preparation of embodiment 1 calcium ferrite
[0053] (a) Grind phosphogypsum hemihydrate with a moisture content of 3wt% and pyrite with a moisture content of 15wt% evenly, the molar ratio of the active ingredient ferrous disulfide in the pyrite and the active ingredient calcium sulfate in the phosphogypsum is 0.4:1, adding iron supplement is ferric oxide, and the molar ratio of calcium sulfate in ferric oxide and gypsum is 0.5:1, to obtain a mixed material;
[0054] (b) Put the mixed material into a reactor at a temperature of 950°C, and roast it for 4 hours under a protective atmosphere (nitrogen, carbon monoxide and sulfur dioxide), and cool the solid phase to obtain calcium ferrite, and produce sulfuric acid from the tail gas of sulfur dioxide.
[0055] In Example 1, the decomposition rate of pyrite was 95%, and the decomposition rate of phosphogypsum was 90%. The molar ratio of iron element: calcium element in the prepared calcium ferrite was 2.1:1.
Embodiment 2
[0056] The preparation of embodiment 2 calcium ferrite
[0057] (a) Grind anhydrous phosphogypsum with a moisture content of 0.1wt% and pyrite with a moisture content of 10wt% evenly. The ratio is 0.1:1, the iron supplement added is ferrous oxide, and the molar ratio of ferrous oxide to calcium sulfate in gypsum is 2:1 to obtain a mixed material;
[0058] (b) Put the mixed material into a reactor at a temperature of 1100°C, and roast it for 2.0 hours under a protective atmosphere (nitrogen, carbon dioxide, and sulfur dioxide). The solid phase is cooled to obtain calcium ferrite, and sulfur dioxide tail gas is produced to produce sulfuric acid.
[0059] In Example 2, the decomposition rate of pyrite was 99%, and the decomposition rate of phosphogypsum was 95%. The molar ratio of iron element: calcium element in the prepared calcium ferrite was 2.21:1.
PUM
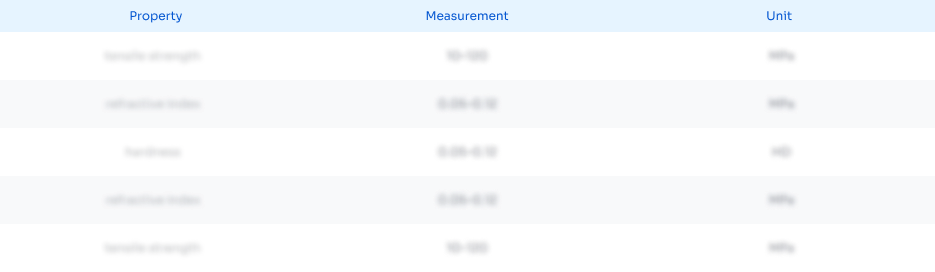
Abstract
Description
Claims
Application Information

- R&D
- Intellectual Property
- Life Sciences
- Materials
- Tech Scout
- Unparalleled Data Quality
- Higher Quality Content
- 60% Fewer Hallucinations
Browse by: Latest US Patents, China's latest patents, Technical Efficacy Thesaurus, Application Domain, Technology Topic, Popular Technical Reports.
© 2025 PatSnap. All rights reserved.Legal|Privacy policy|Modern Slavery Act Transparency Statement|Sitemap|About US| Contact US: help@patsnap.com