Method for direct production of high-grade zinc oxide from zinc material containing high chlorine and fluorine
A direct method, zinc oxide technology, applied in the direction of improving process efficiency, etc., can solve the problems of high production cost, failure to meet the standard of high-grade zinc oxide, and zinc oxide product quality can not meet the standard, so as to achieve low production cost and high manufacturing efficiency. Good performance of slag and good physical performance of agglomerates
- Summary
- Abstract
- Description
- Claims
- Application Information
AI Technical Summary
Problems solved by technology
Method used
Examples
Embodiment 1
[0033] The steps of this embodiment are as follows:
[0034] 1) The raw material composed of high chlorine and fluorine-containing zinc material and furnace ash is mixed with fuel anthracite pulverized coal at a weight ratio of 100:34:75, crushed, added with binder, mixed and rolled to form balls Group; Make the zinc content of the pellets be 32%, and the carbon content be 35%;
[0035] 2) After the bottom charcoal in the zinc-oxygen furnace is red hot, put the pellets in step 1) which has been naturally air-dried for two days into the zinc-oxygen furnace, blow air and release exhaust gas for 10 minutes, and the air volume is controlled at 20% of the total air volume , so that harmful metals such as lead and cadmium and low melting point substances enter the exhaust gas powder;
[0036] 3) After closing the gate, the blast air volume entering the zinc-oxygen furnace increases from small to large. Within half an hour, the furnace temperature of the zinc-oxygen furnace is raise...
Embodiment 2
[0040] The steps of this embodiment are as follows:
[0041] 1) The raw material composed of high chlorine and fluorine-containing zinc material and furnace ash is mixed with fuel anthracite pulverized coal at a weight ratio of 100:27:81, crushed, added with binder, mixed and rolled to form balls Group; Make the zinc content of the pellets be 33.5%, and the carbon content be 34%;
[0042]2) After the bottom charcoal in the zinc-oxygen furnace is red hot, put the pellets in step 1) which has been naturally air-dried for two days into the zinc-oxygen furnace, blow air and release exhaust gas for 12 minutes, and the air volume is controlled at 20% of the total air volume , so that harmful metals such as lead and cadmium and low melting point substances enter the exhaust gas powder;
[0043] 3) After closing the gate, the blast air volume entering the zinc-oxygen furnace increases from small to large, and the furnace temperature of the zinc-oxygen furnace is raised to 1200±20°C w...
Embodiment 3
[0047] The steps of this embodiment are as follows:
[0048] 1) The raw material composed of high chlorine and fluorine-containing zinc material and furnace ash is mixed with fuel anthracite pulverized coal at a weight ratio of 100:18:95, crushed, added with binder, mixed and rolled to form balls Group; Make the zinc content of the pellets be 38%, and the carbon content be 30%;
[0049] 2) After the bottom charcoal in the zinc-oxygen furnace is red hot, put the pellets in step 1) that have been air-dried for two days into the zinc-oxygen furnace, blow air, and release exhaust gas for 15 minutes, and the air volume is controlled at 25% of the total air volume. , so that harmful metals such as lead and cadmium and low melting point substances enter the exhaust gas powder;
[0050] 3) After closing the gate, the blast air volume entering the zinc-oxygen furnace increases from small to large, and the furnace temperature of the zinc-oxygen furnace is raised to 1300±20°C within hal...
PUM
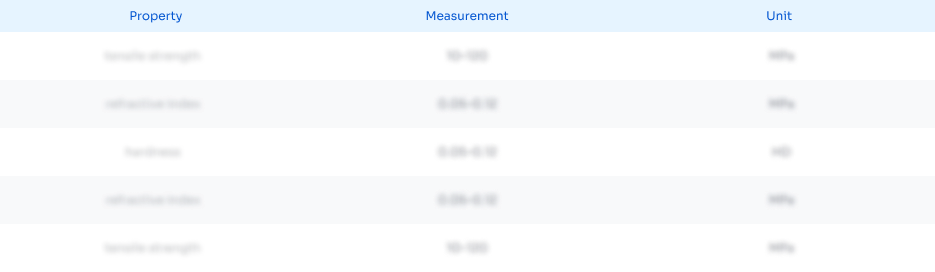
Abstract
Description
Claims
Application Information

- Generate Ideas
- Intellectual Property
- Life Sciences
- Materials
- Tech Scout
- Unparalleled Data Quality
- Higher Quality Content
- 60% Fewer Hallucinations
Browse by: Latest US Patents, China's latest patents, Technical Efficacy Thesaurus, Application Domain, Technology Topic, Popular Technical Reports.
© 2025 PatSnap. All rights reserved.Legal|Privacy policy|Modern Slavery Act Transparency Statement|Sitemap|About US| Contact US: help@patsnap.com