Method and inhibitor capable of inhibiting foaming of ceramic tile polishing waste in high-temperature sintering
A high-temperature sintering and polishing waste slag technology, which is applied in the field of architectural ceramics, can solve the problems of low universality, difficulty in popularization, and complicated process, and achieve the effects of wide applicability, good suppression effect, and simple preparation process
- Summary
- Abstract
- Description
- Claims
- Application Information
AI Technical Summary
Problems solved by technology
Method used
Examples
Embodiment 1
[0036] Embodiment 1-a method for suppressing high-temperature sintering foaming of ceramic tile polishing sludge, comprising the steps of:
[0037] (1) Firstly, take the ceramic tile body raw material, ceramic tile polishing waste residue and inhibitor to prepare a mixture, wherein, according to mass percentage, it includes 20% ceramic tile polishing waste residue, 70% ceramic tile body raw material and 10% inhibitor;
[0038] The inhibitor is wollastonite, and the raw materials of the ceramic tile body are kaolin, illite, A-grade black mud, Huadu black mud, Longshan potassium sand, Guiguang high-aluminum potassium sodium sand, high-aluminum potassium sand, and Guangxi potassium sand. Sand and talc; said ceramic tile polishing waste slag comprises by mass percentage: 65% SiO 2 , 19%Al 2 o 3 , 0.7% CaO, 3% MgO, 3% K 2 O, 4%Na 2 O and 5% SiC;
[0039] (2) Add the mixture prepared in step (1) into a ball mill, and obtain a slurry by wet ball milling. The ball milling particl...
Embodiment 2
[0047] Embodiment 2-a method for suppressing high-temperature sintering and foaming of ceramic tile polishing sludge, comprising the steps of:
[0048] (1) Firstly, take the ceramic tile body raw material, ceramic tile polishing waste residue and inhibitor to prepare a mixture, which includes 10% ceramic tile polishing waste residue, 60% ceramic tile body raw material and 20% inhibitor according to mass percentage;
[0049] The inhibitor is aluminum hydroxide, and the raw materials of the ceramic tile body are kaolin, bentonite, A-grade black mud, Fogang black mud, Yangjiang aluminum potassium sand, Fugang sodium sand, high aluminum potassium sand, Guangxi potassium sand and talc ; The ceramic tile polishing waste slag comprises by mass percentage: 69% SiO 2 , 17%Al 2 o 3 , 0.9% CaO, 2% MgO, 2.5% K 2 O, 3%Na 2 O and 5% SiC;
[0050] (2) Add the mixture prepared in step (1) into a ball mill, and obtain a slurry by wet ball milling, the ball milling particle size of the slu...
Embodiment 3
[0055] Embodiment 3-a method for suppressing high-temperature sintering and foaming of ceramic tile polishing sludge, comprising the steps of:
[0056] (1) Firstly, take ceramic tile body raw materials, ceramic tile polishing slag and inhibitor to prepare a mixture, which includes 15% ceramic tile polishing slag, 65% ceramic tile body raw material and 20% inhibitor in terms of mass percentage;
[0057] The inhibitor is quartz, aluminum hydroxide and wollastonite, wherein quartz: aluminum hydroxide: wollastonite=2:1:1; the raw materials of the ceramic tile body are kaolin, illite, Fogang black mud, flower Duhei mud, Longshan potassium sand, Yangjiang aluminum potassium sand, Fugang sodium sand, Guangxi potash sand and talc; the ceramic tile polishing waste slag includes: 65% SiO 2 , 17% Al 2 o 3 , 0.8% CaO, 2% MgO, 2.6% K 2 O, 3%Na 2 O and 9% SiC;
[0058] (2) Add the mixture prepared in step (1) into a ball mill, and obtain a slurry by wet ball milling. The ball milling p...
PUM
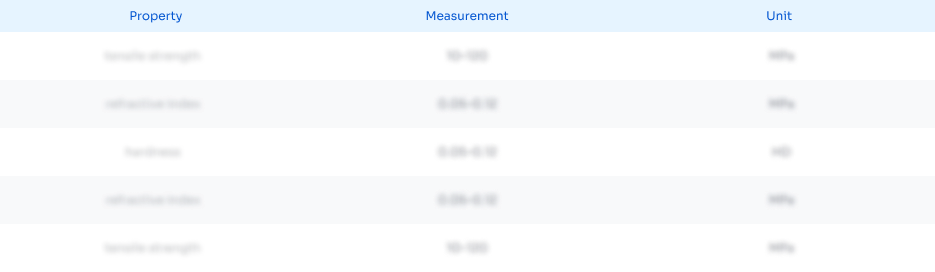
Abstract
Description
Claims
Application Information

- R&D
- Intellectual Property
- Life Sciences
- Materials
- Tech Scout
- Unparalleled Data Quality
- Higher Quality Content
- 60% Fewer Hallucinations
Browse by: Latest US Patents, China's latest patents, Technical Efficacy Thesaurus, Application Domain, Technology Topic, Popular Technical Reports.
© 2025 PatSnap. All rights reserved.Legal|Privacy policy|Modern Slavery Act Transparency Statement|Sitemap|About US| Contact US: help@patsnap.com