Coarse gold wire bonding method
A gold wire bonding and bonding technology, which is applied in the manufacturing of electrical components, electrical solid-state devices, and semiconductor/solid-state devices. And other issues
- Summary
- Abstract
- Description
- Claims
- Application Information
AI Technical Summary
Problems solved by technology
Method used
Image
Examples
Embodiment 1
[0027] Thick gold wire bonding among the present invention adopts thermocompression bonding mode, and its main technical scheme is as follows:
[0028] 1. Selection of bonding welding tools
[0029] Such as figure 2 As shown, in order to facilitate the operation of limiting and applying pressure to the gold wire, the bonding end surface of the welding tool adopts a groove structure 101, and in order to ensure that the damage to the surface of the gold wire during the bonding process is minimized, the grooved type should be selected Soldering tools, and the groove edge should have a rounded structure 102, such as figure 2 Shown is a three-dimensional schematic diagram of the welding end face of the welding tool. figure 2 Among them, the groove structure 101 of the bonding end surface of the welding tool adopts a circular arc structure, the groove diameter D is 110%-120% of the diameter d of the bonded gold wire, and the groove depth H is 30%-40% of the diameter d of the bo...
Embodiment 2
[0038] On the basis of the foregoing embodiments, further, as Figure 2-Figure 8 Shown, a kind of coarse gold wire bonding method, wherein, comprises the following steps:
[0039] Step 1: Set the bonding end surface of the welding tool to adopt a groove structure 101, and the edge of the groove should have a rounded structure 102;
[0040] Step 2: place the processed gold wire 201 on the pad of the thin film circuit substrate;
[0041] Step 3: Place the thin film circuit substrate together with the gold wire 201 on a heating table at 150°C for heating, and at the same time turn on the bonding equipment, heat the soldering tool with a heating coil at a heating temperature of 150°C, and perform bonding after the heating is stable;
[0042] Step 4: Manual bonding is used during bonding, and pressure is applied for bonding to deform the gold wire to a predetermined range.
[0043] The groove structure in the step 1 is an arc structure.
[0044] The groove diameter of the groove...
PUM
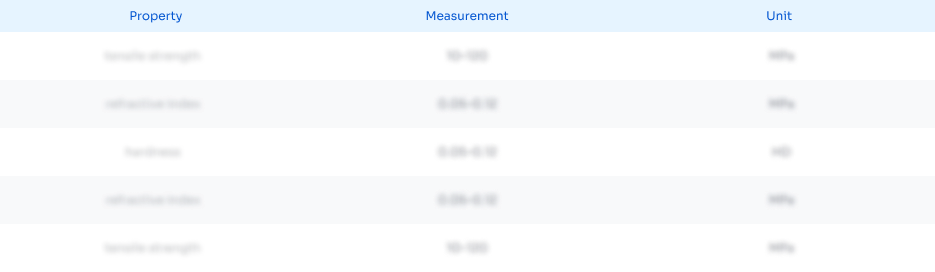
Abstract
Description
Claims
Application Information

- R&D Engineer
- R&D Manager
- IP Professional
- Industry Leading Data Capabilities
- Powerful AI technology
- Patent DNA Extraction
Browse by: Latest US Patents, China's latest patents, Technical Efficacy Thesaurus, Application Domain, Technology Topic, Popular Technical Reports.
© 2024 PatSnap. All rights reserved.Legal|Privacy policy|Modern Slavery Act Transparency Statement|Sitemap|About US| Contact US: help@patsnap.com