Heat treatment method of cold work die steel used for blanking die
A heat treatment method and technology for cold work die steel, applied in the field of iron and steel metallurgy, can solve the problems of shortened service life, can not meet the needs of use, etc., and achieve the effects of low cost, good fatigue resistance and spalling performance, and good toughness
- Summary
- Abstract
- Description
- Claims
- Application Information
AI Technical Summary
Problems solved by technology
Method used
Examples
Embodiment 1
[0012] A heat treatment method for cold working die steel for blanking dies, the chemical composition of the die steel consists of the following components in weight percentage: C: 0.50, Si: 0.2, Mn: 1.5, Cr: 3.4, Mo: 0.7, Ni: 1.3, Ti: 0.02, Nb: 0.6, B: 0.03, V: 0.6, Al: 0.04, S≤0.015, P≤0.025, the balance is Fe and unavoidable impurities; the heat treatment method is: first , put the die steel into the heating furnace, heat it up to 860°C and keep it warm for 4 hours; then, cool it to 450°C and let it air cool; then heat it in the heating furnace to 1010°C and keep it warm for 4 hours; then, After cooling to 920°C, keep it warm for 1.5 hours; then, cool it in quenching oil at a temperature of 30°C; finally, heat it in a heating furnace to 290°C, keep it warm for 6 hours, and then cool it to 100°C, then take it out of the furnace and let it cool in air.
Embodiment 2
[0014] A heat treatment method for cold working die steel for blanking dies, the chemical composition of the die steel consists of the following components in weight percentage: C: 0.54, Si: 0.1, Mn: 1.7, Cr: 3.2, Mo: 0.9, Ni: 1.1, Ti: 0.04, Nb: 0.4, B: 0.05, V: 0.4, Al: 0.06, S≤0.015, P≤0.025, the balance is Fe and unavoidable impurities; the heat treatment method is: first, Put the mold steel into the heating furnace, heat it up to 870°C and keep it warm for 2 hours; then, cool it to 450°C and then take it out of the furnace for air cooling; then heat it to 1030°C in the heating furnace and keep it warm for 2 hours; After reaching 930°C, keep it warm for 0.5 hours; then, cool it in quenching oil with a temperature of 60°C; finally, heat it in a heating furnace to 270°C, keep it warm for 7 hours, and then cool it to 100°C and then take it out of the furnace and let it cool in air.
Embodiment 3
[0016] A heat treatment method for cold working die steel for blanking dies, the chemical composition of the die steel consists of the following components in weight percentage: C: 0.52, Si: 0.15, Mn: 1.6, Cr: 3.3, Mo: 0.8, Ni: 1.2, Ti: 0.03, Nb: 0.5, B: 0.04, V: 0.5, Al: 0.05, S≤0.015, P≤0.025, the balance is Fe and unavoidable impurities; the heat treatment method is: first , put the die steel into the heating furnace, heat it up to 865°C and keep it warm for 3 hours; then, cool it to 450°C and let it cool in air; then heat it in the heating furnace to 1020°C and keep it warm for 3 hours; After cooling to 925°C, keep it warm for 1 hour; then, cool it in quenching oil at a temperature of 45°C; finally, heat it in a heating furnace to 280°C, keep it warm for 6.5 hours, and then cool it to 100°C, then take it out of the furnace and let it cool in air.
PUM
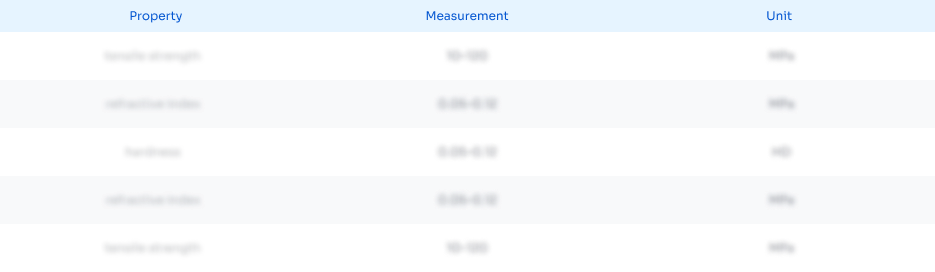
Abstract
Description
Claims
Application Information

- R&D Engineer
- R&D Manager
- IP Professional
- Industry Leading Data Capabilities
- Powerful AI technology
- Patent DNA Extraction
Browse by: Latest US Patents, China's latest patents, Technical Efficacy Thesaurus, Application Domain, Technology Topic, Popular Technical Reports.
© 2024 PatSnap. All rights reserved.Legal|Privacy policy|Modern Slavery Act Transparency Statement|Sitemap|About US| Contact US: help@patsnap.com