Preparation method of welding steel plate with large energy input
A technology for large line energy welding and steel plate, applied in the field of iron and steel metallurgy, can solve problems such as difficulty in meeting the requirements of high-strength steel ultra-large line energy welding performance, improve welding efficiency and construction progress, huge direct and indirect economic benefits, excellent mechanics Effects of performance and welding performance
- Summary
- Abstract
- Description
- Claims
- Application Information
AI Technical Summary
Problems solved by technology
Method used
Examples
Embodiment 1
[0019] A method for preparing a high heat input welded steel plate, the steel plate is composed of the following components in weight percentage: C: 0.12, Mn: 1.6, Si: 0.8, Ni: 1.7, Cr: 0.4, V: 0.03, Ti: 0.05, P≤0.020, S≤0.015, O: 0.005, Als: 0.005, Ca: 0.025, and the rest are Fe and unavoidable impurities. The preparation method includes the following steps: desulfurization treatment of molten steel, converter or electric furnace smelting, ladle furnace Or ladle blowing argon refining, continuous casting, and rolling into plates. During converter or electric furnace smelting, ferrovanadium, ferronickel, and ferro-titanium are added with scrap steel in front of the furnace; ferrochrome and calcium wire are added during the refining period to make the steel The chemical composition meets the requirements of the composition of the steel plate, wherein the temperature of the molten steel entering the mold during continuous casting is controlled at 1530°C, and the rolled plate incl...
Embodiment 2
[0021] A method for preparing a high heat input welded steel plate, the steel plate is composed of the following components in weight percentage: C: 0.16, Mn: 1.2, Si: 1.0, Ni: 1.5, Cr: 0.6, V: 0.01, Ti: 0.15, P≤0.020, S≤0.015, O: 0.001, Als: 0.025, Ca: 0.005, and the rest are Fe and unavoidable impurities. The preparation method includes the following steps: desulfurization treatment of molten steel, converter or electric furnace smelting, ladle furnace Or ladle blowing argon refining, continuous casting, and rolling into plates. During converter or electric furnace smelting, ferrovanadium, ferronickel, and ferro-titanium are added with scrap steel in front of the furnace; ferrochrome and calcium wire are added during the refining period to make the steel The chemical composition meets the requirements of the composition of the steel plate, wherein the temperature of the molten steel entering the mold during continuous casting is controlled at 1550°C, and the rolled plate incl...
Embodiment 3
[0023] A method for preparing a high heat input welded steel plate, the steel plate is composed of the following components in weight percentage: C: 0.14, Mn: 1.4, Si: 0.9, Ni: 1.6, Cr: 0.5, V: 0.02, Ti: 0.10, P≤0.020, S≤0.015, O: 0.003, Als: 0.015, Ca: 0.015, and the rest are Fe and unavoidable impurities. The preparation method includes the following steps: desulfurization treatment of molten steel, converter or electric furnace smelting, ladle furnace Or ladle argon blowing refining, continuous casting, rolling into plates, wherein during converter or electric furnace smelting, ferro-vanadium, ferronickel, and ferro-titanium are added with scrap steel in front of the furnace; ferrochrome and calcium wire are added during the refining period to make the steel The chemical composition meets the composition requirements of the steel plate, wherein the temperature of the molten steel entering the mold during continuous casting is controlled at 1540°C, and the rolled plate includ...
PUM
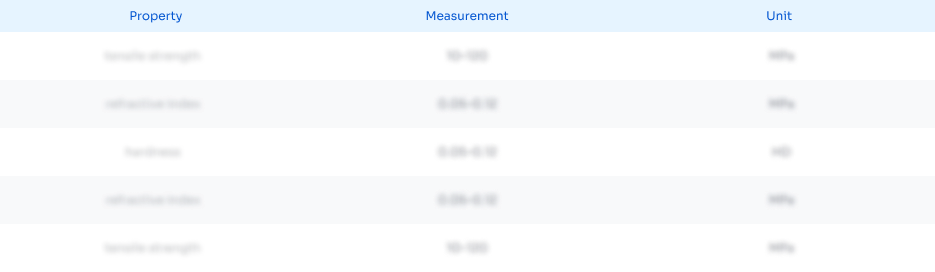
Abstract
Description
Claims
Application Information

- R&D
- Intellectual Property
- Life Sciences
- Materials
- Tech Scout
- Unparalleled Data Quality
- Higher Quality Content
- 60% Fewer Hallucinations
Browse by: Latest US Patents, China's latest patents, Technical Efficacy Thesaurus, Application Domain, Technology Topic, Popular Technical Reports.
© 2025 PatSnap. All rights reserved.Legal|Privacy policy|Modern Slavery Act Transparency Statement|Sitemap|About US| Contact US: help@patsnap.com