Iron catalyst for preparing butadiene through n-butene oxydehydrogenation and preparation method and application of iron catalyst
An oxidative dehydrogenation and iron catalyst technology, which is applied in metal/metal oxide/metal hydroxide catalysts, physical/chemical process catalysts, chemical instruments and methods, etc., can solve the problem of easy powder loss and low catalyst wear resistance. and other problems, to achieve the effect of low amplification risk, high butadiene selectivity and yield, and high catalytic activity
- Summary
- Abstract
- Description
- Claims
- Application Information
AI Technical Summary
Problems solved by technology
Method used
Image
Examples
Embodiment 1
[0016] Ferric nitrate, zinc nitrate, aluminum chloride, nitric acid and water are mixed and dissolved in a certain proportion to form a mixed metal salt solution, and then ammonia water and mixed metal salt solution are added dropwise to the precipitation tank at a certain speed, and the slurry in the precipitation tank needs to be fully stirred to precipitate The temperature of the slurry is controlled at 10.0°C, and the pH value of the precipitation slurry is controlled at 5.0. After the precipitation is completed, the pH value is maintained and the stirring and aging is continued for 120 minutes. The catalyst was flaked into granules, and then activated at 650.0°C for 8 hours. The prepared catalyst was numbered A. The mass ratio of iron (Fe) / zinc (Zn) in the catalyst was 5.02:1, and the mass content of aluminum (Al) was 0.001%. is oxygen (O), see Table 1 and Table 2 for the comparison of the adiabatic reaction performance of the catalyst and the comparison catalyst.
Embodiment 2
[0018] Ferric nitrate, zinc nitrate, nickel nitrate, copper nitrate, barium chloride, cobalt nitrate, nitric acid and water are mixed and dissolved in a certain proportion to form a mixed metal salt solution, and then the ammonium bicarbonate solution is added dropwise into the mixed metal salt solution at a certain speed, The precipitation slurry needs to be fully stirred, the temperature of the precipitation slurry is controlled at 100.0°C, and the pH value of the precipitation slurry is controlled at 8.0. After the precipitation is completed, the precipitation slurry is filtered and washed to pH = 6.0-8.0. After the filter cake is dried at 120.0°C for 12 hours, then sliced Particle catalyst, then activated at 800.0°C for 4h, the number of prepared catalyst is B, the mass ratio of iron (Fe) / zinc (Zn) in the catalyst is 6.94:1, the mass content of nickel (Ni) is 0.12%, copper (Cu ) mass content is 0.54%, barium (Ba) mass content is 0.27%, cobalt (Co) mass content is 1.07%, and...
Embodiment 3
[0020] After iron-containing steel, metal zinc and metal copper are dissolved in nitric acid solution, manganese nitrate is added, and a mixed metal salt solution with a certain metal ion ratio is configured as required, and then the ammonia water / urea mixed solution is added dropwise to the mixed metal salt solution at a certain speed, Stir well, control the temperature of the precipitation slurry at 40.0°C, control the pH value of the precipitation end point at 6.50, maintain the pH value after the precipitation end point and continue to stir and age for 60 minutes, filter the precipitation slurry and wash until pH = 6.0-8.0, then dry the filter cake at 120.0°C 24h, then chipped into a granular catalyst, and then activated at 550.0°C for 48h. The prepared catalyst was numbered C. The mass ratio of iron (Fe) / zinc (Zn) in the catalyst was 1.21:1, and the mass content of copper (Cu) was 0.05 %, the mass content of manganese (Mn) is 1.00%, and the rest is oxygen (O). The adiabati...
PUM
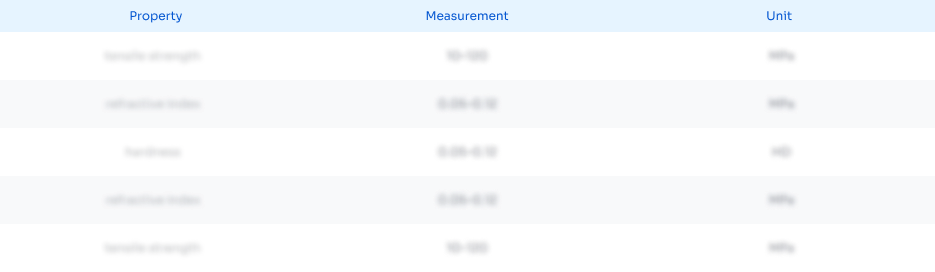
Abstract
Description
Claims
Application Information

- R&D
- Intellectual Property
- Life Sciences
- Materials
- Tech Scout
- Unparalleled Data Quality
- Higher Quality Content
- 60% Fewer Hallucinations
Browse by: Latest US Patents, China's latest patents, Technical Efficacy Thesaurus, Application Domain, Technology Topic, Popular Technical Reports.
© 2025 PatSnap. All rights reserved.Legal|Privacy policy|Modern Slavery Act Transparency Statement|Sitemap|About US| Contact US: help@patsnap.com