Vitrified particulate heat-insulated material for walls
A technology of vitrified microbeads and thermal insulation materials, applied in the field of building materials, can solve the problems of poor harmful gas aging resistance and weather resistance, high water absorption, flammable and fireproof performance, etc., and achieve the effect of improving comprehensive performance and construction performance.
- Summary
- Abstract
- Description
- Claims
- Application Information
AI Technical Summary
Problems solved by technology
Method used
Examples
Embodiment 1
[0020] A vitrified microbead wall thermal insulation material, the vitrified microbead wall thermal insulation material comprises the following components: 100 parts of vitrified microspheres, 50 parts of expanded perlite, 50 parts of cement, 30 parts of water glass, solidified 3 parts of water-repellent agent, 5 parts of water-repellent agent, and 3 parts of penetrating agent.
[0021] The production process of the vitrified microbead wall insulation material comprises the following steps:
[0022] (1) Weigh vitrified microbeads, expanded perlite, cement, water glass, curing agent, water repellent, and penetrating agent according to the stated ratio, put them into a mixer and mix them evenly;
[0023] (2) Add distilled water to the above mixture, and continue stirring with a mixer for 30 minutes;
[0024] (3) Pour the above slurry into the mold and use a press molding machine to press and form, wherein the pressure of the press is set to 0.80MPa, the pressing time is set to ...
Embodiment 2
[0026] A vitrified microbead wall thermal insulation material, the vitrified microbead wall thermal insulation material comprises the following components: 120 parts of vitrified microspheres, 50 parts of expanded perlite, 30 parts of cement, 50 parts of water glass, solidified 3 parts of agent, 3 parts of water-repellent agent, 3 parts of penetrating agent.
[0027] The production process of the vitrified microbead wall insulation material comprises the following steps:
[0028] (1) Weigh vitrified microbeads, expanded perlite, cement, water glass, curing agent, water repellent, and penetrating agent according to the stated ratio, put them into a mixer and mix them evenly;
[0029] (2) Add distilled water to the above mixture, and continue stirring with a mixer for 40 minutes;
[0030] (3) Pour the above slurry into the mold and use a press molding machine to press and form, wherein the pressure of the press is set to 0.80MPa, the press time is set to 40min, and finally the ...
Embodiment 3
[0032] A vitrified microbead wall thermal insulation material, the vitrified microbead wall thermal insulation material comprises the following components: 110 parts of vitrified microspheres, 50 parts of expanded perlite, 40 parts of cement, 20 parts of water glass, solidified 5 parts of water-repellent agent, 5 parts of water-repellent agent, and 3 parts of penetrating agent.
[0033] The production process of the vitrified microbead wall insulation material comprises the following steps:
[0034] (1) Weigh vitrified microbeads, expanded perlite, cement, water glass, curing agent, water repellent, and penetrating agent according to the stated ratio, put them into a mixer and mix them evenly;
[0035] (2) Add distilled water to the above mixture, and continue stirring with a mixer for 40 minutes;
[0036] (3) Pour the above slurry into the mold and use a press molding machine to press and form, wherein the pressure of the press is set to 0.80MPa, the press time is set to 40m...
PUM
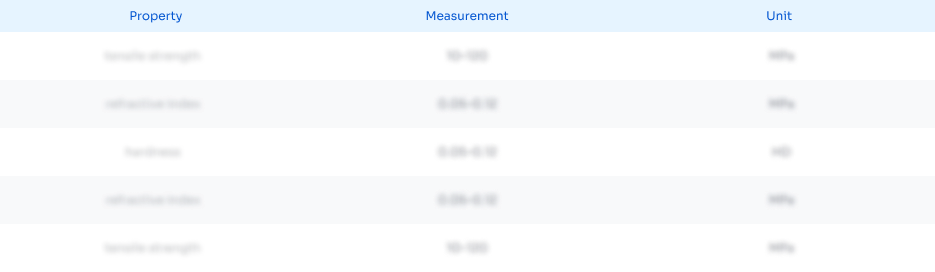
Abstract
Description
Claims
Application Information

- R&D Engineer
- R&D Manager
- IP Professional
- Industry Leading Data Capabilities
- Powerful AI technology
- Patent DNA Extraction
Browse by: Latest US Patents, China's latest patents, Technical Efficacy Thesaurus, Application Domain, Technology Topic, Popular Technical Reports.
© 2024 PatSnap. All rights reserved.Legal|Privacy policy|Modern Slavery Act Transparency Statement|Sitemap|About US| Contact US: help@patsnap.com