Two-dimensional porous graphitized carbon-coated nickel-tin alloy material and preparation and application thereof
A nickel-tin alloy and graphitized carbon technology, which is applied in electrical components, battery electrodes, circuits, etc., can solve the problems of unsatisfactory electrode cycle performance and rate performance, unfavorable lithium ion and electron transmission, and low degree of graphitization of carbon materials. , to achieve the effect of excellent shape, strong controllability and good cycle performance
- Summary
- Abstract
- Description
- Claims
- Application Information
AI Technical Summary
Problems solved by technology
Method used
Image
Examples
Embodiment 1
[0024] Weigh 2.5g citric acid, 0.495g nickel nitrate and 9.8gNaCl, dissolve the mixture in 50ml of deionized water, stir and dissolve with a magnetic stirrer with a stirring speed of 300r / min to form a solution, and then use a 400W ultrasonic Sonicate for 15 minutes and mix well. Put the mixed solution into a vacuum drying oven at 80° C. for vacuum drying until a mixture is obtained. Grind the mixture, take 6g of the mixed powder and put it in the ark A, put the ark in the tube furnace, take 1g of stannous chloride and put it in the ark B, put the ark B into the tube furnace, make it stick to the ark A , 200ml / min of Ar inert gas was introduced for 30min to exclude the air, and then the temperature was raised to 650℃ with 200ml / min of Ar inert gas at a heating rate of 10℃ / min, and the temperature was kept for 0.5h for carbonization and gas phase exchange reaction. After completion, it was cooled to room temperature under the protection of Ar atmosphere to obtain a calcined pr...
Embodiment 2
[0027]Weigh 5g of citric acid, 0.495g of nickel nitrate and 19.6g of NaCl, dissolve the mixture in 100ml of deionized water, stir and dissolve with a magnetic stirrer at a stirring speed of 300r / min to form a solution, and then use a 400W ultrasonic Sonicate for 15 minutes and mix well. Put the mixed solution into a vacuum drying oven at 80° C. for vacuum drying until a mixture is obtained. Grind the mixture, take 10g of the mixed powder and put it in the ark A, put the ark in the tube furnace, take 1g of stannous chloride and put it in the ark B, put the ark B into the tube furnace so that it sticks to the ark A , pass 200ml / min of Ar inert gas to exclude air, then use 200ml / min of Ar inert gas at a heating rate of 10°C / min to raise the temperature to 750°C, keep warm for 1h for carbonization and gas phase exchange reaction, after the reaction Cool to room temperature under the protection of Ar atmosphere to obtain a calcined product. Collect the calcined product, grind it ...
Embodiment 3
[0029] Weigh 1.25g citric acid, 0.495g nickel nitrate and 9.8gNaCl, dissolve the mixture in 50ml of deionized water, stir and dissolve with a magnetic stirrer with a stirring speed of 300r / min to form a solution, and then use a 400W ultrasonic Sonicate for 15 minutes and mix well. Put the mixed solution into a vacuum drying oven at 80° C. for vacuum drying until a mixture is obtained. Grind the mixture, take 12g of the mixed powder and put it in the ark A, put the ark in the tube furnace, take 1g of stannous chloride and put it in the ark B, put the ark B into the tube furnace, make it stick to the ark A , pass 200ml / min of Ar inert gas to exclude air, then use 200ml / min of Ar inert gas at a heating rate of 10°C / min to raise the temperature to 700°C, keep warm for 1.5h for carbonization and gas phase exchange reaction, and the reaction is over Afterwards, it was cooled to room temperature under the protection of Ar atmosphere to obtain a calcined product. Collect the calcine...
PUM
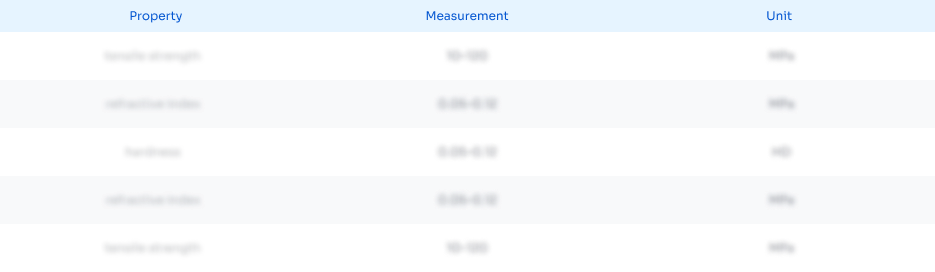
Abstract
Description
Claims
Application Information

- R&D
- Intellectual Property
- Life Sciences
- Materials
- Tech Scout
- Unparalleled Data Quality
- Higher Quality Content
- 60% Fewer Hallucinations
Browse by: Latest US Patents, China's latest patents, Technical Efficacy Thesaurus, Application Domain, Technology Topic, Popular Technical Reports.
© 2025 PatSnap. All rights reserved.Legal|Privacy policy|Modern Slavery Act Transparency Statement|Sitemap|About US| Contact US: help@patsnap.com