Manufacturing method for printed circuit board
A technology for printed circuit boards and manufacturing methods, which is applied in the direction of multilayer circuit manufacturing and electrical connection formation of printed components, which can solve problems such as low reliability, shortened production cycle, and difficult alignment, so as to reduce wiring density and reduce safety. Distance, the effect of increasing the wiring density
- Summary
- Abstract
- Description
- Claims
- Application Information
AI Technical Summary
Problems solved by technology
Method used
Image
Examples
Embodiment 1
[0055] Step 1, such as Figure 8 As shown, an insulating dielectric material 1 with a protective film is laminated on a metal foil (copper foil) 2 .
[0056] Step 2, such as Figure 9 As shown, a via hole 3 is formed on the above-mentioned insulating dielectric material 1 with a protective film. The hole is generally processed by laser, which can be carbon dioxide laser or UV laser.
[0057] Step 3, such as Figure 10 As shown, the conductive material 4 is filled in the above-mentioned via hole, and then the protective film is removed; the conductive material is generally a paste or slurry containing metal particles, and the metal particles include but are not limited to copper, silver, iron, etc.; the hole filling method can be The conventional ordinary screen printing method can also be used for vacuum screen printing.
[0058] In the 4th step, a metal foil 5 is placed on the surface of the insulating dielectric material 1 filled with the conductive material 4, such as ...
Embodiment 2
[0066] Step 1, such as Figure 19 As shown, an insulating dielectric material 1 with a protective film is laminated on a metal foil (copper foil) 2 .
[0067] Step 2, such as Figure 20 As shown, a via hole 3 is formed on the above-mentioned insulating dielectric material 1 with a protective film. The hole is generally processed by laser, which can be carbon dioxide laser or UV laser.
[0068] Step 3, such as Figure 21 As shown, the conductive material 4 is filled in the above-mentioned via hole 3, and then the protective film is removed; the conductive material is generally a paste or paste containing metal particles, and the metal particles include but are not limited to copper, silver, iron, etc.; the hole filling method You can use the conventional common screen printing method, or you can use vacuum screen printing.
[0069] In the 4th step, a metal foil 5 is placed on the surface of the insulating dielectric material 1 filled with the conductive material 4, such as ...
PUM
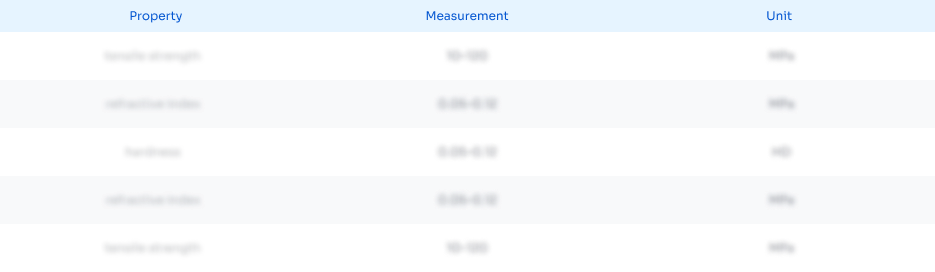
Abstract
Description
Claims
Application Information

- Generate Ideas
- Intellectual Property
- Life Sciences
- Materials
- Tech Scout
- Unparalleled Data Quality
- Higher Quality Content
- 60% Fewer Hallucinations
Browse by: Latest US Patents, China's latest patents, Technical Efficacy Thesaurus, Application Domain, Technology Topic, Popular Technical Reports.
© 2025 PatSnap. All rights reserved.Legal|Privacy policy|Modern Slavery Act Transparency Statement|Sitemap|About US| Contact US: help@patsnap.com