Grinding crack diameter measurement method based on steel ball grinding crack gradient
A technology of diameter measurement and steel ball milling, which is applied in the direction of measuring devices, image data processing, instruments, etc., can solve the problems of time-consuming, labor-intensive, difficult to ensure measurement accuracy, labor-intensive, etc.
- Summary
- Abstract
- Description
- Claims
- Application Information
AI Technical Summary
Problems solved by technology
Method used
Image
Examples
Embodiment Construction
[0070] The wear scar diameter measurement method based on the steel ball wear scar gradient of the present invention specifically comprises the following steps:
[0071] Step S1: Place the steel ball and the white scale in the electronic scanning mirror, use the electronic scanning mirror to collect the color wear pattern F of the steel ball and the white scale to be tested, and input it into the computer, the collected steel The grinding pattern F is a 768×1024 RGB color image, and the scale is selected as a standard type with a nominal value of 0.5mm.
[0072] Step S2: Carry out grayscale processing on the steel ball wear scar image F to obtain a wear scar grayscale image f. The grayscale of the color image F is shown in formula 1:
[0073] f(x,y)=0.3·R(x,y)+0.59·G(x,y)+0.11·B(x,y) (Formula 1)
[0074] Among them, f is the wear spot grayscale image; f(x, y) is the gray value of the pixel (x, y); x and y represent the row and column of the pixel (x, y); 1≤x≤768, 1 ≤y≤1024,...
PUM
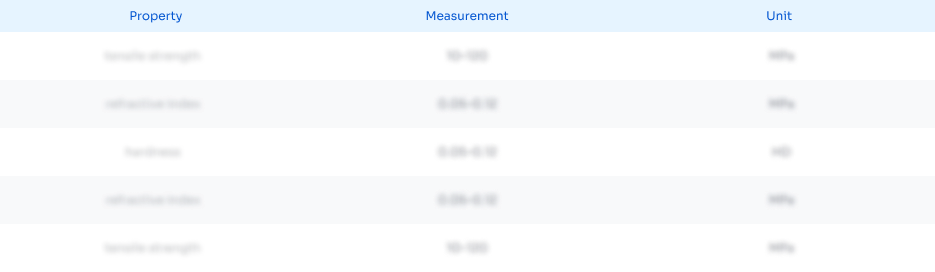
Abstract
Description
Claims
Application Information

- R&D
- Intellectual Property
- Life Sciences
- Materials
- Tech Scout
- Unparalleled Data Quality
- Higher Quality Content
- 60% Fewer Hallucinations
Browse by: Latest US Patents, China's latest patents, Technical Efficacy Thesaurus, Application Domain, Technology Topic, Popular Technical Reports.
© 2025 PatSnap. All rights reserved.Legal|Privacy policy|Modern Slavery Act Transparency Statement|Sitemap|About US| Contact US: help@patsnap.com