Reverse flotation technology of phosphate ore in alkaline medium
An alkaline medium, reverse flotation technology, applied in the field of reverse flotation technology, can solve the problems of serious corrosion of contact equipment, pipeline storage tanks, production can not be carried out normally, easy to generate calcium sulfate scaling, etc., to achieve easy and stable operation, The effect of easy dosing control and adjustment, easy purchase and use
- Summary
- Abstract
- Description
- Claims
- Application Information
AI Technical Summary
Problems solved by technology
Method used
Examples
Embodiment 1
[0022] Embodiment 1, the reverse flotation process of phosphate rock in a kind of alkaline medium, its steps are as follows:
[0023] (1) Crush the phosphate rock and mix it evenly with industrial lime, add 5 kg of industrial lime to each ton of raw ore, mix it into the grinding machine, add water to adjust the slurry to a mass concentration of 30%, and make the mineral composition of the material reach After the monomer is dissociated, it enters the reverse flotation roughing tank, the pulp in the tank is alkaline, and the reverse flotation collector C is added at an amount of 0.1 kg / t raw ore 5-9 Soap is slurried, after sizing, aerated, and reverse flotation roughing is carried out to obtain roughing foam mainly containing carbonate gangue minerals and a part of roughing phosphorus concentrate products;
[0024] (2) The roughing foam enters the reverse flotation concentration tank, and the reverse flotation pH regulator industrial lime with the dosage of 0.5kg / t raw ore and ...
Embodiment 2
[0025] Embodiment 2, the reverse flotation process of phosphate rock in a kind of alkaline medium, its steps are as follows:
[0026] (1) Crush the phosphate rock and mix it evenly with industrial lime. Add 15 kg of industrial lime to each ton of raw ore. After mixing, enter the grinding machine. Add water to adjust the slurry to a mass concentration of 40%, so that the mineral composition of the material reaches After the monomer is dissociated, it enters the reverse flotation roughing tank, the pulp in the tank is alkaline, and the reverse flotation collector C is added at an amount of 0.8 kg / t raw ore 5-9 Soap is slurried, after sizing, aerated, and reverse flotation roughing is carried out to obtain roughing foam mainly containing carbonate gangue minerals and a part of roughing phosphorus concentrate products;
[0027] (2) The roughing foam enters the reverse flotation beneficiation tank, and the reverse flotation pH regulator industrial lime with the dosage of 4 kg / t raw...
Embodiment 3
[0028] Embodiment 3, a kind of reverse flotation process of phosphate rock in alkaline medium, its steps are as follows:
[0029] (1) Crush the phosphate rock and mix it evenly with industrial lime, add 10 kg of industrial lime to each ton of raw ore, mix it into the grinding machine, add water to adjust the slurry to a mass concentration of 35%, and make the mineral composition of the material reach After the monomer is dissociated, it enters the reverse flotation roughing tank, the pulp in the tank is alkaline, and the reverse flotation collector C is added at an amount of 0.5 kg / t raw ore 5-9 Soap is slurried, after sizing, aerated, and reverse flotation roughing is carried out to obtain roughing foam mainly containing carbonate gangue minerals and a part of roughing phosphorus concentrate products;
[0030] (2) The roughing foam enters the reverse flotation beneficiation tank, and the reverse flotation pH regulator industrial lime with the dosage of 2 kg / t raw ore and the ...
PUM
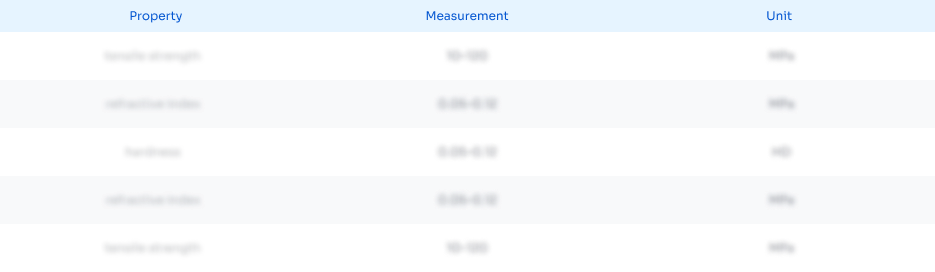
Abstract
Description
Claims
Application Information

- R&D
- Intellectual Property
- Life Sciences
- Materials
- Tech Scout
- Unparalleled Data Quality
- Higher Quality Content
- 60% Fewer Hallucinations
Browse by: Latest US Patents, China's latest patents, Technical Efficacy Thesaurus, Application Domain, Technology Topic, Popular Technical Reports.
© 2025 PatSnap. All rights reserved.Legal|Privacy policy|Modern Slavery Act Transparency Statement|Sitemap|About US| Contact US: help@patsnap.com