Treatment method of laterite-nickel ore
A lateritic nickel ore and treatment method technology, applied in the field of smelting, can solve the problems of low grade nickel production, process environmental pollution, and low reduction temperature, and achieve the effects of increasing output and quality, wide application range, and reducing reduction temperature
- Summary
- Abstract
- Description
- Claims
- Application Information
AI Technical Summary
Problems solved by technology
Method used
Image
Examples
Embodiment 1
[0061] The raw material is laterite nickel ore with a nickel grade of 1.34% by weight and an iron grade of 17.52% by weight. According to the weight ratio of 100 parts by weight of laterite nickel ore, 10 parts by weight of coal, and 10 parts by weight of limestone, the pellets are pressed after being evenly mixed, and the pellets are dried. Put it into a rotary hearth furnace and reduce it for 20min at 1320°C. The high-temperature flue gas discharged from the rotary hearth furnace is returned to the furnace front system for drying of laterite nickel ore raw materials and pellets. The products discharged from the rotary hearth furnace are screened and crushed after water quenching, and the products smaller than 4mm are evenly fed into the jig machine to obtain Nickel-iron grains, tailings after jig sorting are wet-milled in a ball mill, the grinding concentration is controlled to 60% by weight, the particles with a grinding particle size below 0.074mm account for 38.89% by weig...
Embodiment 2
[0065] The raw material is laterite nickel ore with a nickel grade of 1.27% by weight and an iron grade of 21.85% by weight. According to the weight ratio of 100 parts by weight of laterite nickel ore, 15 parts by weight of coal, and 10 parts by weight of limestone, the pellets are pressed after being evenly mixed, and the pellets are dried. Put it into a rotary hearth furnace and reduce it for 15 minutes at 1380°C. The high-temperature flue gas discharged from the rotary hearth furnace is returned to the furnace front system for drying of laterite nickel ore raw materials and pellets. The products discharged from the rotary hearth furnace are screened and crushed after water quenching, and the products smaller than 6mm are evenly fed into the jig machine to obtain Nickel-iron pellets, the tailings after jig sorting are wet-milled in the ball mill, the grinding concentration is controlled to 50% by weight, the particles with a grinding particle size below 0.074mm account for 42...
PUM
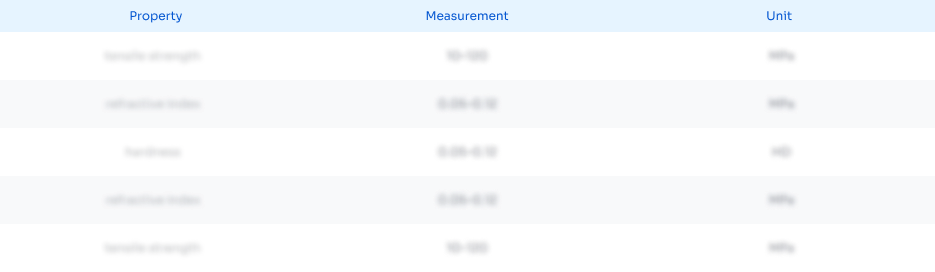
Abstract
Description
Claims
Application Information

- R&D
- Intellectual Property
- Life Sciences
- Materials
- Tech Scout
- Unparalleled Data Quality
- Higher Quality Content
- 60% Fewer Hallucinations
Browse by: Latest US Patents, China's latest patents, Technical Efficacy Thesaurus, Application Domain, Technology Topic, Popular Technical Reports.
© 2025 PatSnap. All rights reserved.Legal|Privacy policy|Modern Slavery Act Transparency Statement|Sitemap|About US| Contact US: help@patsnap.com