Solid catalyst component for preparing ultra-high molecular weight polyethylene
A solid catalyst and ultra-high molecular weight technology, applied in the field of solid catalyst components, can solve the problems of complex preparation process, increased polymer processing difficulty, unsatisfactory particle shape control, etc., and achieves increased reaction capacity, high catalytic activity, Good bulk density
- Summary
- Abstract
- Description
- Claims
- Application Information
AI Technical Summary
Problems solved by technology
Method used
Image
Examples
Embodiment 1
[0030] 1. Preparation of 4,5-bis(dimethylamide)-di-n-butyl phthalate
[0031]
[0032] (a) Reflux 1mmol of pyrene carboxylic acid and 1mmol of ethylene glycol, 2 drops of concentrated sulfuric acid in 50mL of toluene solvent for 1h, and distill off the solvent;
[0033] (b) Reflux the compound obtained in the above steps and 2 mmol hexamethylphosphoric triamide in 50 mL benzene for 30 min, and distill off the solvent;
[0034] (c) Reflux the compound obtained in the above steps and 2 mmol potassium carbonate in a mixed solvent composed of 40 mL ethanol and 5 mL water for 30 min, adjust the pH value of the system to 4 with dilute hydrochloric acid, and evaporate the solvent;
[0035] (d) Reflux the compound obtained in the above steps with 2 mmol of n-butanol and 2 drops of concentrated sulfuric acid in 50 mL of toluene solvent for 1 h, and evaporate the solvent to obtain the compound 4,5-bis(dimethylamide)-phthalic acid di n-Butyl ester; Ms:420.23; 1HNMR (300MHz, CDCl 3 )...
Embodiment 2
[0041] 1. Preparation of 4,5-bis(diethylamide)-diisobutyl phthalate compound
[0042]
[0043] The preparation method of the above compound is the same as in Example 1, except that the hexamethylphosphoric triamide in step (b) is replaced by hexaethylphosphoric triamide, and n-butanol is replaced by isobutanol in step (d).
[0044] 2. Preparation of catalyst components
[0045] Add 2mmol ethoxymagnesium and 200mmol isooctyl alcohol into a reactor fully replaced by nitrogen, and pass CO 2 , stirred for 1.5h; the above solution was added to -20°C 100mmol titanium tetrachloride solution, after the addition was completed, the temperature was slowly raised to 40°C, and 0.1mmol 4,5-bis(diethylamide)-phthalic acid was added Diisobutyl, after stirring for 1 hour, filter and wash to obtain a solid; add 100 mmol titanium tetrachloride and 20 mmol n-butyl titanate mixture to the obtained solid, raise the temperature to 90 ° C, react for 2 hours, filter and wash, Dry in vacuo to obta...
Embodiment 3
[0049] Using the same diester compound, the preparation process of the solid main component of the catalytic body is the same as in Example 1, except that the amount of the diester compound is changed to 0.08 mmol. Polymerization is the same as in Example 1. The results are shown in the table.
PUM
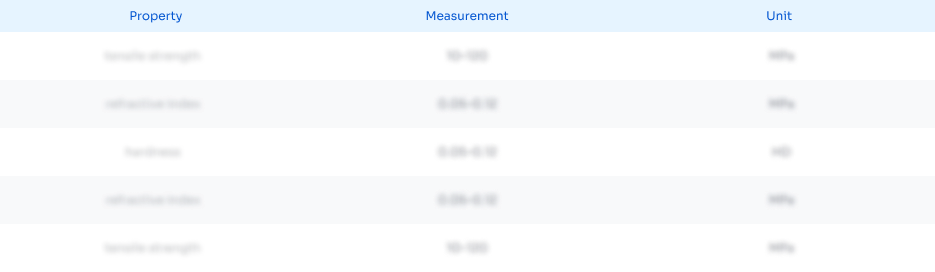
Abstract
Description
Claims
Application Information

- R&D
- Intellectual Property
- Life Sciences
- Materials
- Tech Scout
- Unparalleled Data Quality
- Higher Quality Content
- 60% Fewer Hallucinations
Browse by: Latest US Patents, China's latest patents, Technical Efficacy Thesaurus, Application Domain, Technology Topic, Popular Technical Reports.
© 2025 PatSnap. All rights reserved.Legal|Privacy policy|Modern Slavery Act Transparency Statement|Sitemap|About US| Contact US: help@patsnap.com