Method for preparing aluminum hydroxide by utilizing high-alumina coal ash
A technology of high-aluminum fly ash and aluminum hydroxide, which is applied in chemical industry and metallurgy, comprehensive utilization of solid waste resources, and materials, can solve the problems of large slag production, increased energy and water consumption, and difficult separation of impurities and other problems, to achieve the effect of reducing the content of sodium oxide and alumina, reducing energy consumption and water consumption, and reducing the amount of lye circulation
- Summary
- Abstract
- Description
- Claims
- Application Information
AI Technical Summary
Problems solved by technology
Method used
Image
Examples
Embodiment 1
[0041] 1, the high aluminum fly ash described in Table 1 is mixed with a sodium hydroxide solution with a mass fraction of 15%, and a pre-desilication reaction is carried out in an autoclave, and the liquid-solid ratio of the lye and the high aluminum fly ash is 2:1, the pre-desiliconization reaction temperature is 110°C, and the stirring speed is 600r / min to obtain a mixture of desiliconization liquid whose main component is sodium silicate and pre-desilication fly ash.
[0042] 2. The pre-desiliconized fly ash after filtration and separation is washed and mixed evenly with dilute acid with a concentration of 15% according to the liquid-solid ratio of 2:1, and then added to the reactor lined with polytetrafluoroethylene. Reaction at 50°C for 1.5h. Activate and remove impurities such as iron and titanium, and filter and separate the reaction product after the reaction to obtain pickling solution and pickling activated fly ash.
[0043] 3. After pickling and activating the fly...
Embodiment 2
[0052] 1. High-aluminum fly ash pretreatment Repeat the desiliconization method of the above-mentioned embodiment 1 to obtain desiliconized fly ash and desiliconization liquid.
[0053] 2. After the desiliconized fly ash is washed, it is mixed with a concentrated NaOH solution with a mass fraction of 65% according to a certain ratio, and then added to the high-pressure reactor. Among them, the soda-ash ratio is 4.0:1 (mass ratio), the reaction temperature is 160°C, the reaction time is 3h, and the stirring rate is 600r / min. After the reaction is finished, pour cooling water, cool down to 100°C, and then heat-preserve, filter and separate to obtain crude sodium aluminate solution and primary dissolution slag.
[0054] 3. After the primary dissolution slag is mixed with 65% sodium hydroxide lye and calcium hydroxide, it is added to the high-pressure reactor, and the secondary dissolution reaction is carried out at a high temperature of 220°C. The ratio of alkali to slag is 12:1....
Embodiment 3
[0061] 1. High-aluminum fly ash pretreatment Repeat the desiliconization method of the above-mentioned embodiment 1 to obtain desiliconized fly ash and desiliconization liquid.
[0062] 2. After the desiliconized fly ash is washed, it is mixed with a concentrated NaOH solution with a mass fraction of 40% according to a certain ratio, and then added to the autoclave. Among them, the soda-ash ratio is 3.0:1 (mass ratio), the reaction temperature is 220°C, the reaction time is 1h, and the stirring rate is 600r / min. After the reaction is finished, pour cooling water, cool down to 100°C, and then heat-preserve, filter and separate to obtain crude sodium aluminate solution and primary dissolution slag.
[0063] 3. After the primary dissolution slag is mixed with 40% sodium hydroxide lye and calcium hydroxide, it is added to the high-pressure reactor, and the secondary dissolution reaction is carried out at a high temperature of 220°C. The ratio of alkali to slag is 9:1. The reactio...
PUM
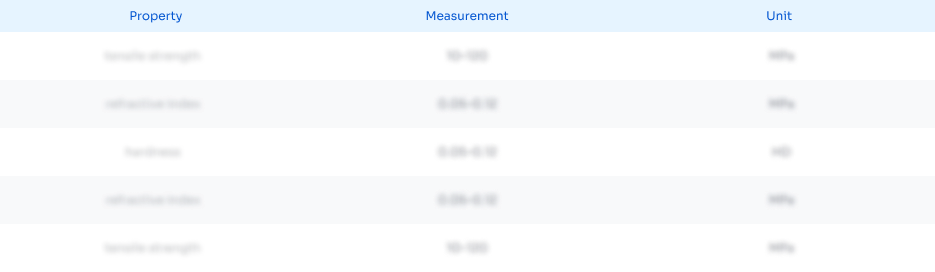
Abstract
Description
Claims
Application Information

- R&D
- Intellectual Property
- Life Sciences
- Materials
- Tech Scout
- Unparalleled Data Quality
- Higher Quality Content
- 60% Fewer Hallucinations
Browse by: Latest US Patents, China's latest patents, Technical Efficacy Thesaurus, Application Domain, Technology Topic, Popular Technical Reports.
© 2025 PatSnap. All rights reserved.Legal|Privacy policy|Modern Slavery Act Transparency Statement|Sitemap|About US| Contact US: help@patsnap.com