Three-phase alternating-current ore smelting furnace and method for controlling furnace condition thereof
A three-phase AC and control method technology, which is applied in the field of three-phase AC submerged arc furnace and three-phase AC submerged arc furnace condition control, can solve problems such as difficulty in furnace extraction, poor furnace condition stability, and furnace condition varies from person to person. Achieve the effects of expanding the area of the reaction layer and the melting layer, improving the utilization rate of electric energy, and high utilization rate of electric energy
- Summary
- Abstract
- Description
- Claims
- Application Information
AI Technical Summary
Problems solved by technology
Method used
Image
Examples
Embodiment 1
[0035] see image 3 with Figure 4 , is a three-phase AC submerged arc furnace of the present invention, which is a three-phase three-electrode AC submerged arc furnace, including a furnace body 1, three electrodes 2A, 2B, 2C vertically arranged in the furnace, and three electrodes 2A, 2B, and 2C arranged in the furnace. The high-temperature-resistant insulation device 3', the electrodes 2A, 2B, and 2C are inserted into the charge in the furnace, and during smelting, the charge is heated by the current of the electrodes 2A, 2B, and 2C, and the charge layer 4, the reaction layer 5, and the melting layer are sequentially formed from top to bottom. Layer 6, wherein the lower ends of the electrodes 2A, 2B, and 2C correspond to the reaction layer 5, and the liquid product of the molten layer 5 flows out from the furnace outlet 10. The high-temperature-resistant insulating device 3' is composed of three high-temperature-resistant insulating plates. The three electrodes The hearth o...
Embodiment 2
[0037] see Figure 5 with Image 6 , is another three-phase AC submerged arc furnace of the present invention, which is a three-phase six-electrode AC submerged arc furnace, including a furnace body 1, electrodes 2A vertically arranged in the hearth of the three-phase AC submerged arc furnace, 2B, 2C and 2X, 2Y, 2Z and the high temperature resistant insulation device 3' arranged in the furnace, the electrodes 2A, 2B, 2C and 2X, 2Y, 2Z are inserted into the charge in the furnace, during smelting, the charge is covered by the electrodes 2A, 2B , 2C and 2X, 2Y, and 2Z are heated by electric current, and form a charge layer 4, a reaction layer 5, and a melting layer 6 sequentially from top to bottom, wherein the lower ends of the electrodes 2A, 2B, 2C and 2X, 2Y, and 2Z correspond to the reaction layer 5 , the liquid product of the molten layer 6 flows out from the furnace outlet 10, and the high-temperature-resistant insulating device 3' is composed of five high-temperature-resi...
PUM
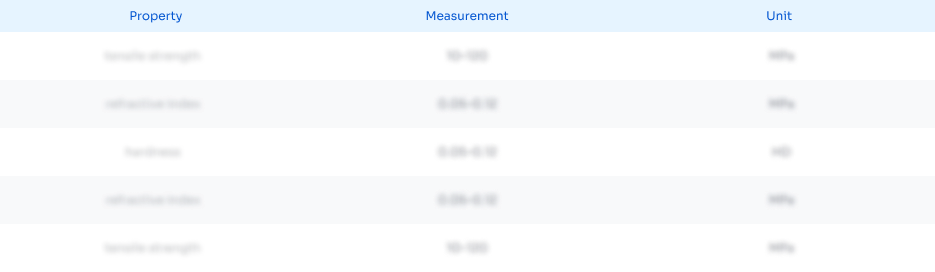
Abstract
Description
Claims
Application Information

- R&D
- Intellectual Property
- Life Sciences
- Materials
- Tech Scout
- Unparalleled Data Quality
- Higher Quality Content
- 60% Fewer Hallucinations
Browse by: Latest US Patents, China's latest patents, Technical Efficacy Thesaurus, Application Domain, Technology Topic, Popular Technical Reports.
© 2025 PatSnap. All rights reserved.Legal|Privacy policy|Modern Slavery Act Transparency Statement|Sitemap|About US| Contact US: help@patsnap.com