Low-porosity periclase-magnesium aluminate spinel-zirconia sintered composite refractory material and production process thereof
A magnesia-aluminum spinel and refractory technology, which is applied in the field of periclase-magnesium-aluminum spinel-zirconia sintered composite refractory materials, can solve the problems of increasing the purchase cost of refractory materials and being unacceptable to glass manufacturers.
- Summary
- Abstract
- Description
- Claims
- Application Information
AI Technical Summary
Problems solved by technology
Method used
Image
Examples
Embodiment 1
[0016] Sintered magnesia with 97% MgO content and synthetic magnesia-alumina spinel with 66% alumina content and 34% magnesium oxide content are used as main materials, and the proportion is: 5-1mm sintered magnesia 45%, 1-0.088mm sintered Magnesia 22%, 3 , apparent porosity 14.2%, load softening temperature T 0.6 = 1680°C, thermal shock stability 1100°C water cooling ≥ 8 times, a refractory material with good high temperature resistance, thermal shock resistance, low porosity physics and ideal chemical mineral composition has been produced.
Embodiment 2
[0018] Fused magnesia with 97% MgO content and synthetic magnesia-alumina spinel with 66% alumina content and 34% magnesia content are used as main materials, and the ratio is: 5-1mm fused magnesia 40%, 1-0.088 mm synthetic magnesium aluminum spinel 25%, 3 , apparent porosity 12.8%, load softening temperature T 0.6 >1700°C, thermal shock stability 1100°C water cooling = 2 times, a refractory material with good physical and chemical properties and ideal chemical mineral composition was prepared.
PUM
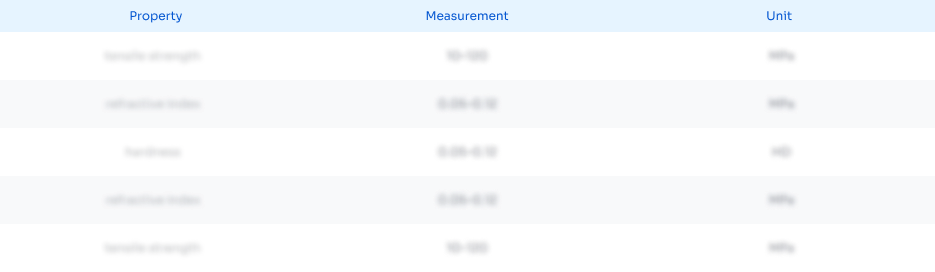
Abstract
Description
Claims
Application Information

- R&D
- Intellectual Property
- Life Sciences
- Materials
- Tech Scout
- Unparalleled Data Quality
- Higher Quality Content
- 60% Fewer Hallucinations
Browse by: Latest US Patents, China's latest patents, Technical Efficacy Thesaurus, Application Domain, Technology Topic, Popular Technical Reports.
© 2025 PatSnap. All rights reserved.Legal|Privacy policy|Modern Slavery Act Transparency Statement|Sitemap|About US| Contact US: help@patsnap.com