Supported copper-manganese composite oxide catalyst capable of removing formaldehyde at room temperature and preparation method
A technology of composite oxides and catalysts, applied in metal/metal oxide/metal hydroxide catalysts, physical/chemical process catalysts, chemical instruments and methods, etc., can solve the limitation of the promotion and application of formaldehyde removal, high price, etc. problem, to achieve the effect of good economy and practicability, low production cost and large processing capacity
- Summary
- Abstract
- Description
- Claims
- Application Information
AI Technical Summary
Problems solved by technology
Method used
Image
Examples
Embodiment 1
[0019] Weigh 1.72gCu(NO 3 ) 2 ·3H 2 O and 10.32g of 50% manganese nitrate aqueous solution were added to distilled water to form a 10% mixed solution, and then 18g of powdered TiO 2 , magnetically stirred at 50°C for 2h, dried at 120°C for 6h, and calcined in a muffle furnace at 1000°C for 3h to obtain the catalyst. In the prepared catalyst, the copper-manganese component has a loading capacity of 10% based on the weight of metal elements, and the molar ratio of Cu and Mn is 1:4.
[0020] Catalyst performance tests are in the attached figure 1 The static catalytic oxidation of formaldehyde shown in the experimental device was carried out. Place 0.5 g of catalyst 1 and sample bottle 2 with a volume of 1 mL at the bottom of a conical flask 5 with a volume of 1 L. At the same time, add 5 μL of 37% formalin solution into the sample bottle 2 and use a silica gel equipped with a balance bag 3 to quickly seal the Erlenmeyer flask 5 and place it in a constant temperature water ba...
Embodiment 2
[0022] Weigh 5.62gCu(NO 3 ) 2 ·3H 2 O and 16.86g of 50% manganese nitrate aqueous solution were added to distilled water to form a 15% mixed solution, and then 16g of powdered TiO 2 , magnetically stirred at 40°C for 4h, dried at 100°C for 8h, and calcined in a muffle furnace at 700°C for 5h to obtain the catalyst. In the prepared catalyst, the copper-manganese component has a loading capacity of 20% in terms of metal element weight, and the molar ratio of Cu and Mn is 1:2.
[0023] Catalyst performance tests are in the attached figure 2The continuous-flow fixed-bed micro-catalytic reaction experimental device was carried out. Dilute 5g of catalyst with quartz sand and fill it in a stainless steel fixed bed 12 (pipe diameter 20mm, length 550mm), compressed air from the air storage tank 7 is controlled by a pressure reducing valve 8 and a flow meter 9 into the conical tank containing the formaldehyde solution. The bottle 5 carries the formaldehyde gas through the buffer b...
Embodiment 3
[0025] Weigh 24.6gCu(NO 3 ) 2 ·3H 2 O and 37.02g of 50% manganese nitrate aqueous solution were added to distilled water to form a 20% mixed solution, and then 28g of powdered TiO 2 , magnetically stirred at 30°C for 6h, dried at 80°C for 10h, and calcined in a muffle furnace at 400°C for 8h to obtain the catalyst. In the prepared catalyst, the copper-manganese component has a loading capacity of 30% based on the weight of metal elements, and the molar ratio of Cu and Mn is 1:1.
[0026] The performance test of the catalyst is the same as in Example 2, but the formaldehyde concentration at the inlet is 100ppm, and the reaction gas flow rate is 400mL min -1 , the reaction temperature is 20°C, and the formaldehyde removal rate is 90.3% calculated by the difference of formaldehyde gas concentration before and after.
PUM
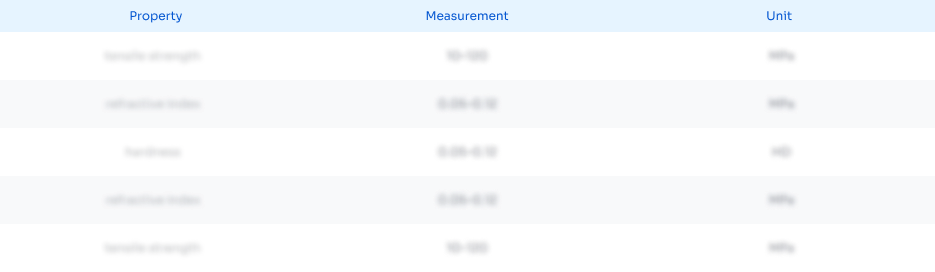
Abstract
Description
Claims
Application Information

- R&D Engineer
- R&D Manager
- IP Professional
- Industry Leading Data Capabilities
- Powerful AI technology
- Patent DNA Extraction
Browse by: Latest US Patents, China's latest patents, Technical Efficacy Thesaurus, Application Domain, Technology Topic, Popular Technical Reports.
© 2024 PatSnap. All rights reserved.Legal|Privacy policy|Modern Slavery Act Transparency Statement|Sitemap|About US| Contact US: help@patsnap.com