A method for efficiently extracting microbial oil
A microbial oil and microbial technology, applied in the direction of fat production, fat oil/fat production, etc., can solve the problems of low single extraction rate, large solvent consumption, low oil extraction rate, etc., and achieve high single extraction rate and solvent consumption The effect of a large amount and a small amount of solvent
- Summary
- Abstract
- Description
- Claims
- Application Information
AI Technical Summary
Problems solved by technology
Method used
Image
Examples
Embodiment 1
[0078] Embodiment 1: Add water to the influence of grease recovery rate
[0079] Mix 628g of algae powder (Schizochytrium sp. self-cultivated and spray-dried, water content 3.2%) with about 3L of n-hexane, and get 2638g of wall-broken mixture after treatment in a sand mill.
[0080] 1. Weigh 4 parts of the broken wall mixture, each about 20g;
[0081] 2. Add different proportions of water respectively and shake well;
[0082] 3. Centrifuge at 6000g for 5 minutes to separate the supernatant, which is mixed oil;
[0083] 4. The mixed oils were desolvated separately and weighed in an oven at 60°C to obtain hairy algal oil.
[0084] Calculate the recovery rate of algae oil, and the results are shown in Table 6.
[0085] Table 6. Algae oil recovery rate
[0086]
Embodiment 2
[0087] Embodiment 2: Add the influence of ethanol aqueous solution on oil recovery rate
[0088] Mix 628g of algae powder (Schizochytrium sp. self-cultivated and spray-dried, water content 3.2%) with about 3L of n-hexane, and get 2638g of wall-broken mixture after treatment in a sand mill.
[0089] 1. Weigh 4 parts of the broken wall mixture, each about 20g;
[0090] 2. Add different proportions of ethanol aqueous solution (the amount of water and ethanol added is shown in Table 7) and shake well;
[0091] 3. Centrifuge at 6000g for 5 minutes to separate the supernatant, which is mixed oil;
[0092] 4. The mixed oils were desolvated separately and weighed in an oven at 60°C to obtain hairy algal oil.
[0093] Calculate the recovery rate of algae oil, and the results are shown in Table 7.
[0094] Table 7. Algae oil recovery rate
[0095]
Embodiment 3
[0096] Embodiment 3: the influence of ethanol solution concentration on oil recovery rate
[0097] Mix 628g of algae powder (Schizochytrium sp. self-cultivated and spray-dried, water content 3.2%) with about 3L of n-hexane, and get 2638g of wall-broken mixture after treatment in a sand mill.
[0098] 1. Weigh 10 parts of the broken wall mixture, each about 20g;
[0099] 2. Add ethanol aqueous solution of different solubility respectively, and shake well, wherein the addition amount of ethanol aqueous solution is 2 times of the weight of algae cell in the broken wall mixture;
[0100] 3. Centrifuge at 2000g for 1min to separate the supernatant, which is mixed oil;
[0101] 4. The mixed oils were desolvated separately and weighed in an oven at 60°C to obtain hairy algal oil.
[0102] Calculate the algae oil recovery rate, and the results are shown in Table 8:
[0103] Table 8. Comparison of the effects of different concentrations of ethanol on the recovery of algae oil
...
PUM
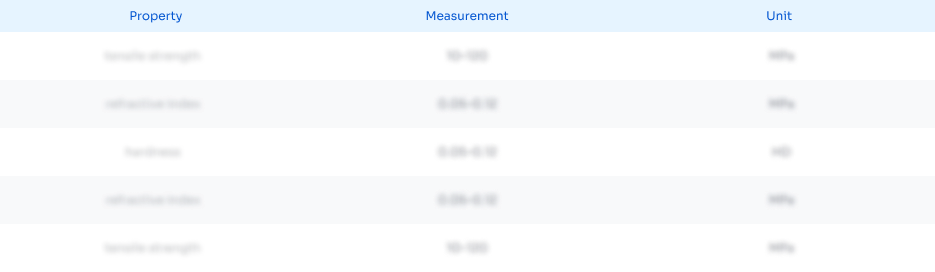
Abstract
Description
Claims
Application Information

- Generate Ideas
- Intellectual Property
- Life Sciences
- Materials
- Tech Scout
- Unparalleled Data Quality
- Higher Quality Content
- 60% Fewer Hallucinations
Browse by: Latest US Patents, China's latest patents, Technical Efficacy Thesaurus, Application Domain, Technology Topic, Popular Technical Reports.
© 2025 PatSnap. All rights reserved.Legal|Privacy policy|Modern Slavery Act Transparency Statement|Sitemap|About US| Contact US: help@patsnap.com