Method and device for recovering sulphur in acidic gas, and reactor
A technology for acid gas and sulfur recovery, which is applied in separation methods, chemical instruments and methods, and separation of dispersed particles. It can solve problems such as failure of sulfur recovery devices, failure of normal operation of combustion furnaces, and large concentration fluctuations, so as to reduce catalysts. Consumption and cost, increasing equipment and investment, and improving sulfur conversion and sulfur recovery effects
- Summary
- Abstract
- Description
- Claims
- Application Information
AI Technical Summary
Problems solved by technology
Method used
Image
Examples
Embodiment 1
[0056] Such as Figure 4 The apparatus shown consists of successively connected hydrohydrolysis reactors R 1 , the first heat exchanger E 1 , catalytic oxidation reactor R 2 , the second heat exchanger E 2 , air heater E 3 , condenser E 4 , liquid sulfur separator V 1 , water separator V 2 And tail gas scrubber C 1 , the second heat exchanger E 2 The shell side outlet and the first heat exchanger E 1 Shell side inlet connection, first heat exchanger E 1 The shell side outlet and hydrohydrolysis reactor R 1 Inlet Connection, Air Heater E 3 The shell side outlet and the catalytic oxidation reactor R 2 connect.
[0057] The above-mentioned hydrohydrolysis reactor R 1 and catalytic oxidation reactor R 2 Both horizontal and vertical reactors can be used.
[0058] The acid gas first passes through the second heat exchanger E 2 , the first heat exchanger E 1 and out of the hydrohydrolysis reactor R 1 The gas heat exchange raises the temperature, and then enters the...
Embodiment 2
[0060] achieve as figure 1 During the shown process, the two steps of catalytic hydrogenation and catalytic oxidation can be carried out in the same reactor, that is, the design of the present invention is as follows: Figure 5 In the horizontal reactor shown, the interior of the reactor is divided into two chambers by a vertical partition: adiabatic hydrolysis reaction chamber R 1a and water-cooled heat exchange catalytic oxidation reaction chamber R 2a , the acid gas from the hydrolysis reaction chamber R 1a The top enters, and the hydrogenation hydrolysis reaction is carried out in the catalyst layer. The organic sulfur in the acid gas is hydrolyzed into inorganic sulfides, and the reactor starts from the hydrogenation catalytic reaction chamber R 1a The bottom exits the reactor, and then enters the catalytic oxidation reaction chamber R 2a Carry out catalytic oxidation reaction, catalytic oxidation reaction chamber R 2a The inside is a water-cooled heat exchange reacto...
Embodiment 3
[0062] achieve as figure 2 In the process shown, the first three steps of catalytic oxidation, catalytic hydrogenation and second catalytic oxidation can be carried out in the same reactor, using such as Figure 6 In the horizontal reactor shown, the interior of the reactor is divided into three chambers by two vertical partitions, and the middle chamber is the hydrolysis reaction chamber R 1a , the two sides are respectively the first catalytic oxidation reaction chamber R 2a and the second catalytic oxidation reaction chamber R 2b .
[0063] Acid gas advanced first catalytic oxidation reaction chamber R 1a , part of the hydrogen sulfide reacts with oxygen to generate sulfur and water, and then enters the hydrolysis reaction chamber R 1a Carry out catalytic hydrogenation reaction, hydrolyze organic sulfur into inorganic sulfide, and acid gas enters the second catalytic oxidation reaction chamber R 2b The second catalytic oxidation reaction is carried out to catalyticall...
PUM
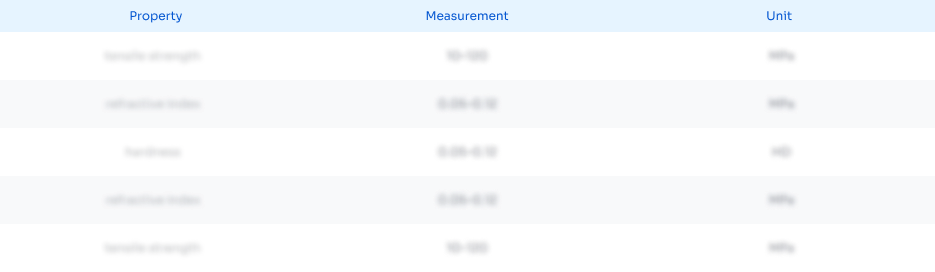
Abstract
Description
Claims
Application Information

- Generate Ideas
- Intellectual Property
- Life Sciences
- Materials
- Tech Scout
- Unparalleled Data Quality
- Higher Quality Content
- 60% Fewer Hallucinations
Browse by: Latest US Patents, China's latest patents, Technical Efficacy Thesaurus, Application Domain, Technology Topic, Popular Technical Reports.
© 2025 PatSnap. All rights reserved.Legal|Privacy policy|Modern Slavery Act Transparency Statement|Sitemap|About US| Contact US: help@patsnap.com