Method used for high efficient separation and enrichment of tin from nickel-tin-iron alloy waste material
A technology for separation and enrichment of ferroalloy, applied in the field of high-efficiency separation and enrichment of tin from nickel-tin-iron alloy waste, it can solve the problems of complex operation, equipment corrosion, environmental pollution, etc., and achieve the effect of simple operation, short process and high quality
- Summary
- Abstract
- Description
- Claims
- Application Information
AI Technical Summary
Problems solved by technology
Method used
Image
Examples
Embodiment 1
[0017] Put nickel-tin-iron alloy waste (its main chemical composition is (unit: mass fraction): Fe=30, Sn=15, Ni=55) in an electric furnace, heat up to 1550°C, and the waste begins to mix and melt; after the waste is fully melted , under an inert gas atmosphere with a pressure of 0.1MPa, the pyrite is blown into the molten pool according to 10% of the mass of the nickel-tin-iron alloy waste through the spray gun, and the sulfidation and detinning reaction is carried out. The high-temperature flue gas generated during the process is recovered after being cooled. Contains tin fume.
[0018] After dust collection, it is discharged into the atmosphere. After analysis and detection, the tin content in the obtained nickel-iron alloy was reduced to 1.8%, and the tin recovery rate reached 88.00%.
Embodiment 2
[0020] Put nickel-tin-iron alloy waste (its main chemical composition is (unit: mass fraction): Fe=35, Sn=18, Ni=47) in an electric furnace, heat up to 1570°C, and the waste begins to mix and melt; after the waste is fully melted , under an inert gas atmosphere with a pressure of 1MPa, pyrite and sulfur are blown into the molten pool through a spray gun according to 20% of the mass of nickel-tin-iron alloy waste, to carry out sulfidation and detinning reaction, and the high-temperature flue gas generated during the process is cooled. Recycling which contains tin fumes.
[0021] After dust collection, it is discharged into the atmosphere. After analysis and detection, the tin content in the obtained nickel-iron alloy was reduced to 1.1%, and the tin recovery rate reached 92.67%.
Embodiment 3
[0023] Put nickel-tin-iron alloy waste (its main chemical composition is (unit: mass fraction): Fe=30, Sn=15, Ni=55) in an intermediate frequency furnace, raise the temperature to 1650°C, and the waste begins to mix and melt; wait until the waste is fully melted Finally, under an inert gas atmosphere with a pressure of 0.5 MPa, nickel sulfide is blown into the molten pool according to 25% of the mass of nickel-tin-iron alloy waste through a spray gun to carry out sulfidation and detinning reaction. The high-temperature flue gas generated during the process is recovered after being cooled. Contains tin fume.
[0024] After dust collection, it is discharged into the atmosphere. After analysis and detection, the tin content in the obtained nickel-iron alloy was reduced to 0.8%, and the tin recovery rate reached 94.67%.
PUM
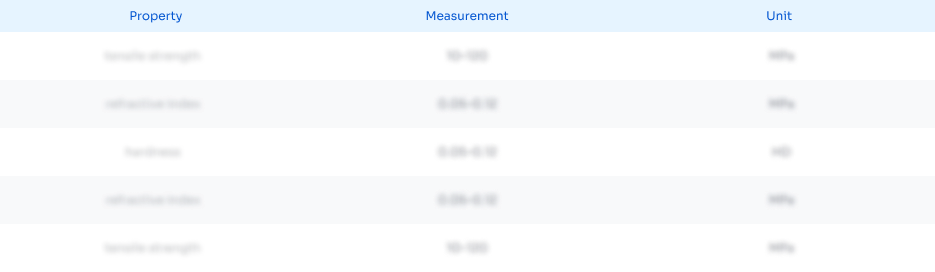
Abstract
Description
Claims
Application Information

- R&D Engineer
- R&D Manager
- IP Professional
- Industry Leading Data Capabilities
- Powerful AI technology
- Patent DNA Extraction
Browse by: Latest US Patents, China's latest patents, Technical Efficacy Thesaurus, Application Domain, Technology Topic, Popular Technical Reports.
© 2024 PatSnap. All rights reserved.Legal|Privacy policy|Modern Slavery Act Transparency Statement|Sitemap|About US| Contact US: help@patsnap.com