Polyamide, synthesis method and application thereof, and polyamide product
A synthesis method and polyamide technology are applied in the field of polyamide, polyamide products, and their synthesis, which can solve the problems of easy degradation and damage to mechanical properties, and achieve the effects of increasing viscosity and inhibiting loss.
- Summary
- Abstract
- Description
- Claims
- Application Information
AI Technical Summary
Problems solved by technology
Method used
Examples
preparation example Construction
[0035] The invention discloses a synthesis method of polyamide, which is characterized in that it comprises the following steps:
[0036] Adding: adding the raw materials into the reaction kettle and mixing thoroughly to obtain a mixture, the raw materials include (a) dibasic acid, (b) diamine, and optionally (c) other components;
[0037] Inflating: Fill the reactor with protective gas, wherein the protective gas contains CO 2 , CO 2 Accounting for the volume content of the protective gas is 60-66.7 or 66.7-100%;
[0038] Prepolymerization: Heating the reactor to make the mixture in the reactor undergo prepolymerization.
[0039] Wherein, after the prepolymerization reaction is completed and the material is discharged, the prepolymerization product is dried and then solid-phase thickened to obtain polyamide.
[0040] Wherein, in the inflation step, the pressure in the reactor is increased to 0.1-0.3MPa, 0.3-0.5MPa or 0.5-1.0MPa.
[0041] Wherein, the protective gas furthe...
Embodiment 1
[0066] Add 20mol of terephthalic acid, 20.2mol of 1,10-decanediamine, 74.8g of benzoic acid, and 6.98g of hypophosphorous acid into a pressure vessel equipped with magnetic coupling stirring, condenser, gas phase port, feeding port, and pressure explosion-proof port Sodium, filled with CO after evacuation 2 to atmospheric pressure, and then filled with CO after repeated vacuuming 2 process three times, and finally the CO 2 The pressure rises to 0.1MPa. The temperature was raised to 220°C with stirring over 2 hours, the reaction mixture was stirred at 220°C for 1 hour, then the temperature of the reactants was raised to 230°C with stirring. The reaction was continued for 2 hours at a constant temperature of 230°C and a constant pressure of 2.2MPa, and the pressure was kept constant by removing the formed water. After the reaction was completed, the material was discharged, and the prepolymer was vacuum-dried at 80°C for 24 hours to obtain the prepolymer. Polymerized product,...
Embodiment 2
[0069] Add 20mol of terephthalic acid, 20.2mol of 1,10-decanediamine, 74.8g of benzoic acid, and 6.98g of hypophosphorous acid into a pressure vessel equipped with magnetic coupling stirring, condenser, gas phase port, feeding port, and pressure explosion-proof port Sodium, filled with CO after evacuation 2 to atmospheric pressure, and then filled with CO after repeated vacuuming 2 process three times, and finally the CO 2 The pressure rose to 0.3MPa. The temperature was raised to 220°C with stirring over 2 hours, the reaction mixture was stirred at 220°C for 1 hour, then the temperature of the reactants was raised to 230°C with stirring. The reaction was continued at a constant temperature of 230°C and a constant pressure of 2.2MPa for 2 hours, and the pressure was kept constant by removing the formed water. After the reaction was completed, the material was discharged, and the prepolymer was vacuum-dried at 80°C for 24 hours to obtain the prepolymer. Polymerized product, ...
PUM
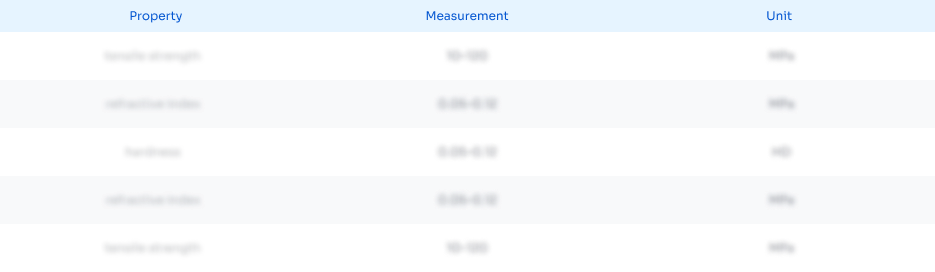
Abstract
Description
Claims
Application Information

- R&D
- Intellectual Property
- Life Sciences
- Materials
- Tech Scout
- Unparalleled Data Quality
- Higher Quality Content
- 60% Fewer Hallucinations
Browse by: Latest US Patents, China's latest patents, Technical Efficacy Thesaurus, Application Domain, Technology Topic, Popular Technical Reports.
© 2025 PatSnap. All rights reserved.Legal|Privacy policy|Modern Slavery Act Transparency Statement|Sitemap|About US| Contact US: help@patsnap.com