Preparation method of epoxy composite material with low packing content, high thermal conductivity and ternary nano/micro structure
A composite material and epoxy technology, applied in the field of epoxy composite material preparation, can solve the problems of deteriorating mechanical and processing properties, high filler content of composite materials, weak thermal conductivity, etc., achieve excellent mechanical and processing properties, and reduce manufacturing costs. , the effect of a complete thermal network
- Summary
- Abstract
- Description
- Claims
- Application Information
AI Technical Summary
Problems solved by technology
Method used
Image
Examples
Embodiment 1
[0033] This embodiment relates to a method for preparing a low filler content, high thermal conductivity ternary nano-microstructure epoxy composite material, comprising the following steps:
[0034] Step (1), Al 2 o 3 , BN surface grafted γ-aminopropyltriethoxysilane (γ-APS)
[0035] Weigh 2g Al 2 o 3 , fully dispersed in 100mL xylene, then added 1wt% γ-APS and stirred and refluxed for 1h; after the reaction was completed, it was centrifuged at high speed, and the product was washed with xylene for 3 times and vacuum-dried at 50°C for 1d to obtain Al 2 o 3 -APS. BN undergoes two steps of pretreatment before grafting silane coupling agent: first, weigh 2g of BN, stir and disperse in 100mL of 30wt% hydrochloric acid solution, react at 50°C for 1h, filter and wash with deionized water for 3 times; Acidified BN was added to 50mL of 30wt% hydrogen peroxide, reacted at 50°C for 1h, then continued to heat up to 75°C for 1h, and the product was centrifuged and dried in vacuum a...
Embodiment 2
[0041] This embodiment relates to a method for preparing a low filler content, high thermal conductivity ternary nano-microstructure epoxy composite material, comprising the following steps:
[0042] Step (1), Al 2 o 3 , BN surface grafted γ-aminopropyltriethoxysilane (γ-APS)
[0043] Weigh 5g Al 2 o 3 , fully dispersed in 200mL xylene, then added 2wt% γ-APS and stirred and refluxed for 2h; after the reaction was completed, it was centrifuged at high speed, and the product was washed with xylene for 3 times and vacuum-dried at 50°C for 1d to obtain Al 2 o 3 -APS. BN undergoes two steps of pretreatment before grafting silane coupling agent: first, weigh 5g of BN, stir and disperse in 200mL of 30wt% hydrochloric acid solution, react at 50°C for 1h, filter and wash with deionized water for 3 times; Acidified BN was added to 100mL 30wt% hydrogen peroxide, reacted at 50°C for 1h, then continued to heat up to 75°C for 1h, the product was centrifuged and dried in vacuum at 50°C...
Embodiment 3
[0049] This embodiment relates to a method for preparing a low filler content, high thermal conductivity ternary nano-microstructure epoxy composite material, comprising the following steps:
[0050] Step (1), Al 2 o 3 , BN surface grafted γ-aminopropyltriethoxysilane (γ-APS)
[0051] Weigh 2g Al 2 o 3 , fully dispersed in 100mL xylene, then added 1wt% γ-APS and stirred and refluxed for 1h; after the reaction was completed, it was centrifuged at high speed, and the product was washed with xylene for 3 times and vacuum-dried at 50°C for 1d to obtain Al 2 o 3 -APS. BN undergoes two steps of pretreatment before grafting silane coupling agent: first, weigh 2g of BN, stir and disperse in 100mL of 30wt% hydrochloric acid solution, react at 50°C for 1h, filter and wash with deionized water for 3 times; Acidified BN was added to 50mL of 30wt% hydrogen peroxide, reacted at 50°C for 1h, then continued to heat up to 75°C for 1h, and the product was centrifuged and dried in vacuum a...
PUM
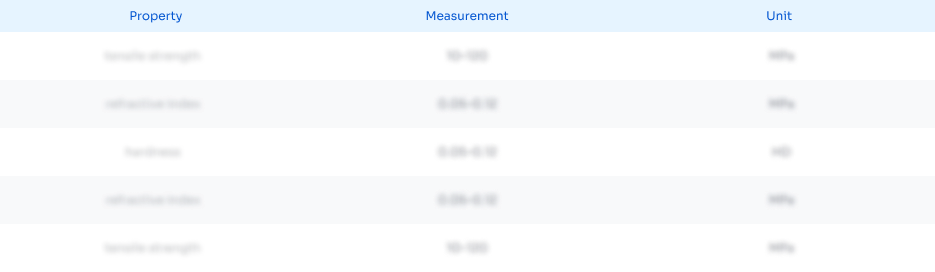
Abstract
Description
Claims
Application Information

- Generate Ideas
- Intellectual Property
- Life Sciences
- Materials
- Tech Scout
- Unparalleled Data Quality
- Higher Quality Content
- 60% Fewer Hallucinations
Browse by: Latest US Patents, China's latest patents, Technical Efficacy Thesaurus, Application Domain, Technology Topic, Popular Technical Reports.
© 2025 PatSnap. All rights reserved.Legal|Privacy policy|Modern Slavery Act Transparency Statement|Sitemap|About US| Contact US: help@patsnap.com