Method for manufacturing water-cooled locomotive cylinder
A water-cooled, cylinder technology, applied in the direction of cylinders, cylinder heads, mechanical equipment, etc., can solve the problems of high consumables, increase costs, and affect efficiency
- Summary
- Abstract
- Description
- Claims
- Application Information
AI Technical Summary
Problems solved by technology
Method used
Image
Examples
Embodiment Construction
[0039] In order to have a more complete and clear disclosure of the technical content used in the present invention, the purpose of the invention and the effects achieved, it will be described in detail below, and please also refer to the disclosed drawings and drawing numbers:
[0040] First, see figure 1 , 2 , Shown in 4,6, is the schematic flow sheet of water-cooled locomotive cylinder method of the present invention, and its steps are as follows:
[0041] A. Molded cylinder base - A cylinder base 1 is molded. The cylinder base 1 has water inlet and outlet holes 11, and a through channel 12 is formed in the center, and a water flow channel is formed around the channel 12. 13, and a protruding wall-adhering section 14 is formed between two adjacent water flow channels 13; the above-mentioned water flow channel 13 is directly provided with a mold core in the mold and molded.
[0042] B. Machining the ring water channel - at the central channel 12 of the cylinder base 1, a ...
PUM
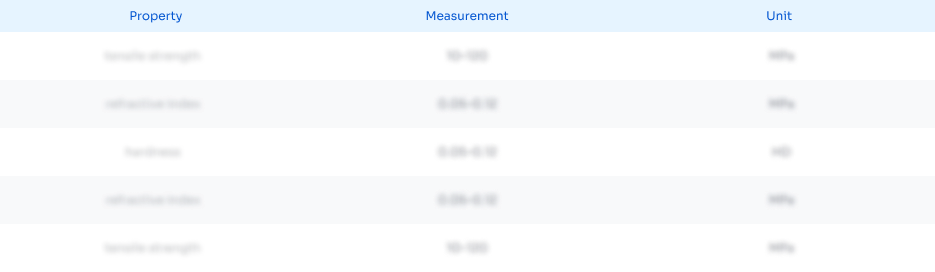
Abstract
Description
Claims
Application Information

- Generate Ideas
- Intellectual Property
- Life Sciences
- Materials
- Tech Scout
- Unparalleled Data Quality
- Higher Quality Content
- 60% Fewer Hallucinations
Browse by: Latest US Patents, China's latest patents, Technical Efficacy Thesaurus, Application Domain, Technology Topic, Popular Technical Reports.
© 2025 PatSnap. All rights reserved.Legal|Privacy policy|Modern Slavery Act Transparency Statement|Sitemap|About US| Contact US: help@patsnap.com