Rail wheel and method for producing a rail wheel
A track and wheel technology, applied in the field of manufacturing track wheels, can solve problems such as insufficient durability
- Summary
- Abstract
- Description
- Claims
- Application Information
AI Technical Summary
Problems solved by technology
Method used
Image
Examples
Embodiment Construction
[0031] exist figure 1 and 2 , the friction disc 2 is installed or assembled on the wheel body 1.
[0032] Here, the spokes 3 of the wheel body 1 have bore holes 8 , which form two circumferential contact surfaces A extending in the radial direction, through which the bolts 6 pass, through which the friction disk 2 and the The wheel body 1 is connected.
[0033] like image 3 As shown, each of a plurality of bolts 6 distributed at the same angular interval on the circumference passes through a fastening hole 5 of the corresponding friction disk 2, which is opposite to the spoke 3 on the end face, such as the cooling fin 4 of the friction disk. Also forms the abutment area.
[0034] Between the abutment area of the fixing hole 5 and the heat sink 4 and the spokes 3, a coating 7 is arranged to match each friction disc 2, the contact surface A of the spoke 3 is on one side, and the contact surface B of the friction disc 2 On the other side it rests against the coating.
[...
PUM
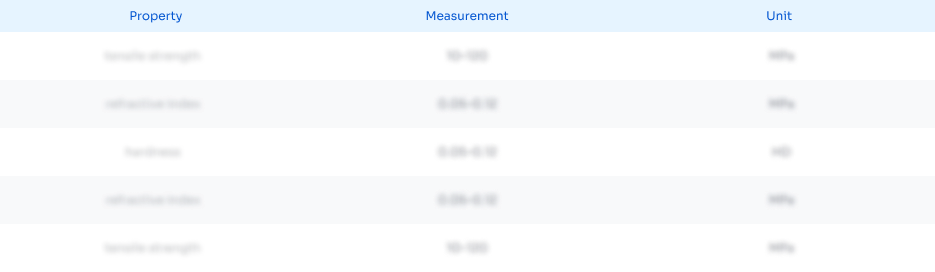
Abstract
Description
Claims
Application Information

- R&D
- Intellectual Property
- Life Sciences
- Materials
- Tech Scout
- Unparalleled Data Quality
- Higher Quality Content
- 60% Fewer Hallucinations
Browse by: Latest US Patents, China's latest patents, Technical Efficacy Thesaurus, Application Domain, Technology Topic, Popular Technical Reports.
© 2025 PatSnap. All rights reserved.Legal|Privacy policy|Modern Slavery Act Transparency Statement|Sitemap|About US| Contact US: help@patsnap.com