Alkali-resistant chopped glass fiber soakage agent
A technology of chopped glass fiber and sizing agent, which is applied in the field of glass fiber surface treatment agent, which can solve the problems of alkali resistance, poor water resistance and wear resistance, failure to meet the use requirements, low strength of cement products, etc., and achieve good alkali resistance Effect
- Summary
- Abstract
- Description
- Claims
- Application Information
AI Technical Summary
Problems solved by technology
Method used
Image
Examples
Embodiment 1
[0051] 1. Put 30 kg of deionized water in the preparation tank, add 0.01 kg of glacial acetic acid and stir well:
[0052] 2. Add 0.1 kg of coupling agent (GE Silicones, A-174 in the United States) and stir, hydrolyze for 30-60 minutes, and it becomes a transparent liquid without oil droplets, and the stirring speed is 60r / m;
[0053] 3. Combine 2.0 kg of polyacrylate film-forming agent (Xi'an Youji Composite Material Co., Ltd., YG5016), 15 kg of epoxy resin emulsion film-forming agent (Xi'an Youji Composite Material Co., Ltd., YG1250) and 1 kg of water-soluble epoxy resin Add film agent (Xi'an Youji Composite Material Co., Ltd., YG801) into the reaction kettle and stir for 10-20min at a stirring speed of 60r / m;
[0054]4. Add the dilution of 0.01 kg of silicone lubricant (Xi'an Zhongchuang Composite Materials Co., Ltd., ZC-315) with 0.1 kg of deionized water at 50-80°C to the preparation tank, and add the dilution with 50-80°C 0.1 kg of deionized water to dilute 0.01 kg of c...
Embodiment 2
[0061] 1. Put 30 kg of deionized water in the preparation tank, add 0.03 kg of glacial acetic acid and stir well:
[0062] 2. Add 0.2 kg of coupling agent (GE Silicones, A-174 in the United States) into the mixture and stir, hydrolyze for 30-60 minutes, it becomes a transparent liquid without oil droplets, and the stirring speed is 60r / m;
[0063] 3. Mix 7.0 kg of polyacrylate film-forming agent (Xi'an Youji Composite Material Co., Ltd., YG5016), 10 kg of epoxy resin emulsion film-forming agent (Xi'an Youji Composite Material Co., Ltd., YG1250) and 3.0 kg of water-soluble epoxy forming agent. Add film agent (Xi'an Youji Composite Material Co., Ltd., YG801) into the reaction kettle and stir for 10-20min at a stirring speed of 60r / m;
[0064] 4. Add the dilution of 0.05 kg of silicone lubricant (Xi'an Zhongchuang Composite Materials Co., Ltd., ZC-315) with 0.5 kg of deionized water at 50-80 ° C to the preparation tank, add the pre-diluted solution with 50-80 ° C 0.5 kg of deion...
Embodiment 3
[0071] 1. Put 30 kg of deionized water in the preparation tank, add 0.04 kg of glacial acetic acid and stir well:
[0072] 2. Add 0.3 kg of coupling agent (GE Silicones, A-174 in the United States) and stir, hydrolyze for 30-60 minutes, and it becomes a transparent liquid without oil droplets, and the stirring speed is 60r / m;
[0073] 3. Mix 6.0 kg of polyacrylate film-forming agent (Xi'an Youji Composite Material Co., Ltd., YG5016), 7.0 kg of epoxy resin emulsion film-forming agent (Xi'an Youji Composite Material Co., Ltd., YG1250) and 7.0 kg of water-soluble epoxy resin Add film agent (Xi'an Youji Composite Material Co., Ltd., YG801) into the reaction kettle and stir for 10-20min at a stirring speed of 60r / m;
[0074] 4. Add the dilution of 0.1 kg of silicone lubricant (Xi'an Zhongchuang Composite Materials Co., Ltd., ZC-315) with 1.0 kg of deionized water at 50-80 ° C to the preparation tank, add the pre-diluted solution with 50-80 ° C 1.0 kg of deionized water to dilute 0...
PUM
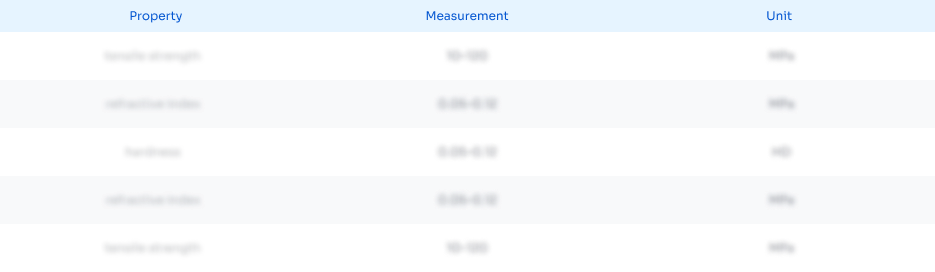
Abstract
Description
Claims
Application Information

- R&D
- Intellectual Property
- Life Sciences
- Materials
- Tech Scout
- Unparalleled Data Quality
- Higher Quality Content
- 60% Fewer Hallucinations
Browse by: Latest US Patents, China's latest patents, Technical Efficacy Thesaurus, Application Domain, Technology Topic, Popular Technical Reports.
© 2025 PatSnap. All rights reserved.Legal|Privacy policy|Modern Slavery Act Transparency Statement|Sitemap|About US| Contact US: help@patsnap.com