Pretreatment process for spinning of kapok loose fibers
A bulk fiber and pre-treatment technology, which is applied in the field of kapok bulk fiber spinning pre-treatment process, can solve problems affecting quality and subsequent processing, and achieve the effects of enhanced hydrophilicity, improved hydrophilic performance, and less environmental pollution
- Summary
- Abstract
- Description
- Claims
- Application Information
AI Technical Summary
Problems solved by technology
Method used
Image
Examples
Embodiment 1
[0019] A kind of kapok bulk fiber spinning pretreatment process, the steps comprise:
[0020] A. Immerse the kapok loose fiber with a smoothing agent for 15 minutes. The smoothing agent is a modified silicone oil smoothing agent, specification XT-01, and the manufacturer is Wuhu Xunteng New Material Co., Ltd.;
[0021] B. Pre-dry the impregnated kapok loose fiber at 55°C for 80s until the water content reaches 5.8%;
[0022] C. Low-temperature plasma treatment is carried out in oxygen atmosphere plasma; the parameters of low-temperature plasma treatment are: discharge time is 40s, and discharge power is 30KW.
[0023] A kapok pure spun combed yarn, using the above-mentioned kapok loose fiber pretreated by low-temperature plasma, after cleaning → carding → pre-doubling → coiling → combing → head-doubling → double-doubling → three-doubling → roving→ Spinning → post-processing and other traditional processes, kapok pure spun combed yarn has 266 twists and 21 fineness.
Embodiment 2
[0025] A kind of kapok bulk fiber spinning pretreatment process, the steps comprise:
[0026] A. Immerse the kapok loose fiber with a smoothing agent for 20 minutes. The smoothing agent is a modified silicone oil smoothing agent, specification XT-01, and the manufacturer is Wuhu Xunteng New Material Co., Ltd.;
[0027] B. Pre-dry the impregnated kapok loose fiber at 100°C for 40s until the water content reaches 4.7%;
[0028] C. Low-temperature plasma treatment is carried out in oxygen atmosphere plasma; the parameters of low-temperature plasma treatment are: discharge time is 150s, and discharge power is 20KW.
[0029] A kapok / long-staple cotton (30 / 70) blended combed yarn, using the above-mentioned kapok loose fibers pretreated by low-temperature plasma, after cleaning → carding → pre-drawing → coiling → combing → end-drawing → Two-fold → three-fold → roving → spun yarn → post-processing and other traditional processes, kapok / long-staple cotton (30 / 70) blended combed yarn h...
Embodiment 3
[0031] A kind of kapok bulk fiber spinning pretreatment process, the steps comprise:
[0032] A. Immerse the kapok loose fiber with a smoothing agent for 25 minutes. The smoothing agent is a modified silicone oil smoothing agent, specification XT-01, and the manufacturer is Wuhu Xunteng New Material Co., Ltd.;
[0033] B. Pre-dry the impregnated kapok loose fiber at 80°C for 60s until the water content reaches 4.5%;
[0034] C. Low-temperature plasma treatment is carried out in oxygen atmosphere plasma; the parameters of low-temperature plasma treatment are: discharge time is 90s, and discharge power is 27KW.
[0035] The processed kapok loose fibers were observed with a scanning electron microscope, as attached figure 1 As shown, it shows that the plasma treatment effect is good.
[0036] A kapok pure spun combed yarn, using the above-mentioned kapok loose fiber pretreated by low-temperature plasma, after cleaning → carding → pre-doubling → coiling → combing → head-doubling...
PUM
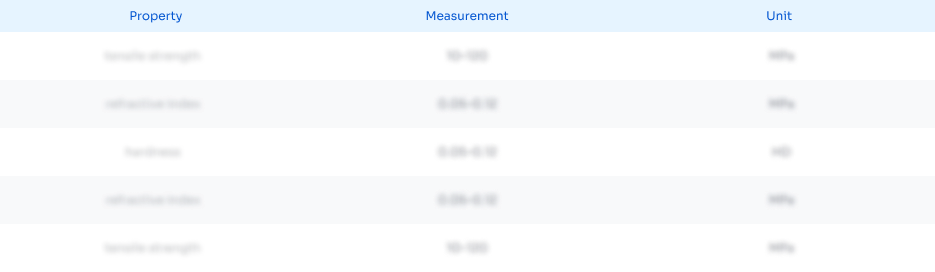
Abstract
Description
Claims
Application Information

- R&D
- Intellectual Property
- Life Sciences
- Materials
- Tech Scout
- Unparalleled Data Quality
- Higher Quality Content
- 60% Fewer Hallucinations
Browse by: Latest US Patents, China's latest patents, Technical Efficacy Thesaurus, Application Domain, Technology Topic, Popular Technical Reports.
© 2025 PatSnap. All rights reserved.Legal|Privacy policy|Modern Slavery Act Transparency Statement|Sitemap|About US| Contact US: help@patsnap.com