Production technique of roller
A production process and roll technology, which is applied in the direction of rolls, metal rolling, manufacturing tools, etc., can solve the problems of difficult production, high production cost, cumbersome process, etc., and achieve the effects of convenient operation, increased yield, and reduced process steps
- Summary
- Abstract
- Description
- Claims
- Application Information
AI Technical Summary
Problems solved by technology
Method used
Examples
Embodiment Construction
[0010] In the production process of the roll of the present invention, the roll includes an alloy outer layer and a core, and the chemical composition weight percentage of the alloy outer layer is: 1.50%≤C2.20%, Si≤0.060%, 0.40%≤Mn≤1.20%, P≤ 0.030%, S≤0.025%, 3.00%≤Cr≤8.00%, Ni≤1.50%, 2.00%≤Mo≤8.00%, 2.00%≤V≤9.00%, W≤3.00%, Nb≤0.85%, Al≤1.20 %, the balance is Fe; the weight percentage of the chemical composition of the core is: 2.8%≤C≤3.4%, 1.8%≤Si≤2.6%, 0.3%≤Mn≤0.6%, P≤0.08%, S≤0.03%, 0.04%≤Mg≤0.06%; the production steps of this roll are: 1) material preparation, leaving a length allowance for hoisting hole processing; 2) processing both ends of the blank; 3) processing the center holes at both ends; 4) top ends, Rough turning; 5) Drilling hoisting holes outside the length of the finished product; 6) Quenching and tempering treatment to make the hardness of the roller body reach 40-50HSD; 7) Correcting the center holes at both ends; 8) Semi-finishing the two ends of the top; ...
PUM
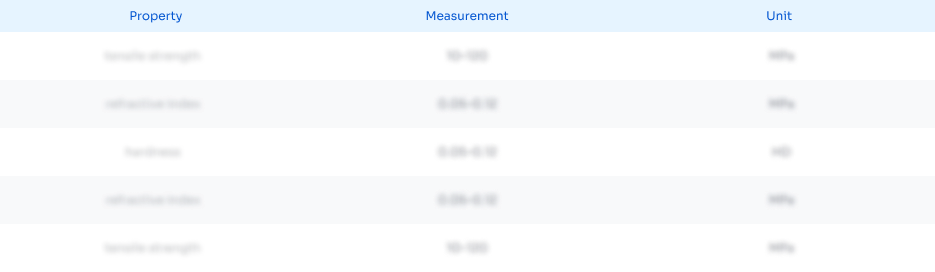
Abstract
Description
Claims
Application Information

- Generate Ideas
- Intellectual Property
- Life Sciences
- Materials
- Tech Scout
- Unparalleled Data Quality
- Higher Quality Content
- 60% Fewer Hallucinations
Browse by: Latest US Patents, China's latest patents, Technical Efficacy Thesaurus, Application Domain, Technology Topic, Popular Technical Reports.
© 2025 PatSnap. All rights reserved.Legal|Privacy policy|Modern Slavery Act Transparency Statement|Sitemap|About US| Contact US: help@patsnap.com