Method for producing chromates through using chromium-containing waste residues
A technology of chromium waste residue and chromate, which is applied in the direction of chromate/dichromate, etc., to achieve the effect of solving environmental pollution, simple process flow and low process cost
- Summary
- Abstract
- Description
- Claims
- Application Information
AI Technical Summary
Problems solved by technology
Method used
Image
Examples
Embodiment 1
[0056] First, a chromium-containing waste slag (dry basis, Cr content 25-30%, V content 0-0.5%, Si content 15-20%) produced during the process of vanadium extraction by vanadium-titanium magnetite was mixed with a concentration of 30 %Na 2 CO 3 The solution was reacted for 4 hours under the conditions of a liquid-solid ratio of 4:1, an oxidant of oxygen, an oxygen pressure of 5atm, and a temperature of 180°C, and the chromium leaching rate was 98%. The leached mixed slurry is filtered and separated to obtain filter cake (II) and chromate-containing alkali solution, and the chromate-containing alkali solution is evaporated and crystallized, and solid-liquid separation is performed to obtain sodium carbonate and sodium chromate crystals. The evaporative crystallization is operated under normal pressure, the initial temperature is 40°C, and the final temperature is 60°C.
Embodiment 2
[0058] Firstly, the chromium-containing waste residue (dry basis, Cr content 25-30%, Al content 0-2%, soluble sulfate 5-10%) of a chromium salt plant water treatment sludge is washed with water slurry, and the liquid-solid ratio (i.e. the mass ratio of the washing solution to the chromium-containing waste residue) is 8:1, and then the filter cake (I) and the washing solution are respectively obtained after gravity sedimentation; the filter cake (I) and the concentration of 75% K 2 CO 3 The solution was reacted for 3 hours under the conditions of a liquid-solid ratio of 10:1, an oxidant of oxygen, an oxygen pressure of 15atm, and a temperature of 150°C, and the chromium leaching rate was 98%. After leaching, the slurry is filtered and separated after impurity removal and desiliconization to obtain filter cake and leachate. The filter cake is washed to obtain non-toxic waste residue; the leaching solution is evaporated and crystallized, and solid-liquid separation is performed ...
Embodiment 3
[0060] Firstly, a chromium-containing waste residue (dry basis, Cr content 15-20%, organic matter content 20-30%, Fe content 0.1-1%) produced by the pharmaceutical industry was ground to a particle size of 20 μm, and the concentration was 10% NaOH countercurrent slurry washing, the liquid-solid ratio (that is, the mass ratio of the washing liquid to the chromium-containing waste residue) is 3:1, and then the filter cake (I) and the washing liquid are obtained after centrifugation, and the washing liquid is evaporated and crystallized to precipitate water-soluble Salt crystals, the secondary steam is condensed and recycled; the filter cake (I) and the NaOH solution with a concentration of 30% are in a liquid-solid ratio of 3:1, the oxidant is oxygen, the oxygen pressure is 2atm, and the temperature is 250°C Under the condition of reaction for 4 hours, the chromium leaching rate is 99%. After leaching, the mixed slurry is centrifuged to obtain filter cake (II) and chromate-conta...
PUM
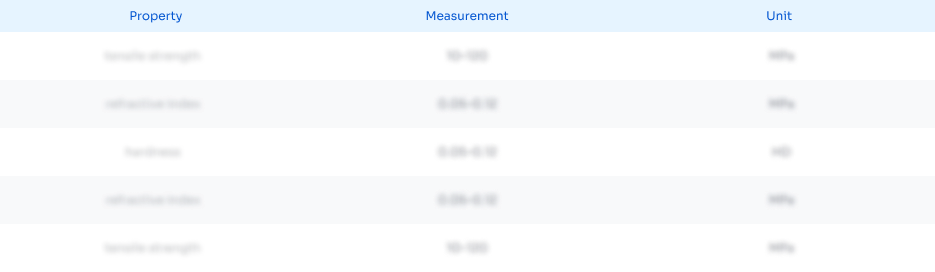
Abstract
Description
Claims
Application Information

- R&D
- Intellectual Property
- Life Sciences
- Materials
- Tech Scout
- Unparalleled Data Quality
- Higher Quality Content
- 60% Fewer Hallucinations
Browse by: Latest US Patents, China's latest patents, Technical Efficacy Thesaurus, Application Domain, Technology Topic, Popular Technical Reports.
© 2025 PatSnap. All rights reserved.Legal|Privacy policy|Modern Slavery Act Transparency Statement|Sitemap|About US| Contact US: help@patsnap.com