Commercial molybdenum oxide ammonia leaching technology capable of reducing slagging rate and molybdenum content in slag
A technology of molybdenum calcination and process, which is applied in the field of ammonia leaching process of molybdenum calcine, can solve the problems of cumbersome molybdenum recovery process, hinder the dissolution of molybdenum trioxide, and troublesome ammonia leaching slag treatment, and achieve strong repeatability and low molybdenum content. Reduce and reduce the effect of slag formation rate
- Summary
- Abstract
- Description
- Claims
- Application Information
AI Technical Summary
Problems solved by technology
Method used
Image
Examples
Embodiment 1
[0024] The present embodiment reduces the slagging rate and the molybdenum calcination ammonia leaching process of molybdenum content in slag comprises the following steps:
[0025] Step 1. Mole ratio Mo:NH 3 =1:2.5, solid-to-liquid ratio 1:2.5 Mix molybdenum calcined sand, ammonia water and deionized water evenly to obtain a suspension, and then stir the suspension at a temperature of 65°C until the pH of the suspension is Be 6.8; The mass percentage concentration of described ammoniacal liquor is 26%, and the mass percentage composition of molybdenum in the described molybdenum calcined sand is 63%;
[0026] Step 2, filtering the suspension with a pH value of 6.8 in step 1 to obtain filter cake and filtrate;
[0027] Step 3: The filter cake described in step 2 is washed with ammonia water with a mass percentage concentration of 26%. The number of washings is 3 times, and the washed filter cake is placed in a drying oven to dry at a drying temperature of 100°C. After 8 hour...
Embodiment 2
[0033] The present embodiment reduces the slagging rate and the molybdenum calcination ammonia leaching process of molybdenum content in slag comprises the following steps:
[0034] Step 1. Mole ratio Mo:NH 3 =1:2, solid-to-liquid ratio 1:2 Mix molybdenum calcined sand, ammonia water and deionized water evenly to obtain a suspension, and then stir the suspension at a temperature of 70°C until the pH of the suspension is Be 7.0; The mass percentage concentration of described ammonia liquor is 28%, and the mass percentage composition of molybdenum in the described molybdenum calcined sand is 61.5%;
[0035] Step 2, filtering the suspension with a pH value of 7.0 in step 1 to obtain filter cake and filtrate;
[0036] Step 3: Wash the filter cake described in Step 2 with ammonia water with a concentration of 28% by mass, the number of washings is 1 time, and place the washed filter cake in a drying oven to dry at a drying temperature of 80°C. After natural cooling for 10 hours, ...
Embodiment 3
[0043] The present embodiment reduces the slagging rate and the molybdenum calcination ammonia leaching process of molybdenum content in slag comprises the following steps:
[0044] Step 1. Mole ratio Mo:NH 3 =1:3, solid-to-liquid ratio 1:3 Mix molybdenum calcined sand, ammonia water and deionized water evenly to obtain a suspension, and then stir the suspension at a temperature of 70°C until the pH of the suspension is Be 6.5; The mass percentage concentration of described ammoniacal liquor is 25%, and the mass percentage composition of molybdenum in the described molybdenum calcined sand is 62.4%;
[0045] Step 2, filtering the suspension with a pH value of 6.5 in step 1 to obtain filter cake and filtrate;
[0046] Step 3: Wash the filter cake described in step 2 with ammonia water with a mass percentage concentration of 27%, the number of washings is 2 times, and place the washed filter cake in a drying oven to dry at a drying temperature of 80°C. After 8 hours of natural...
PUM
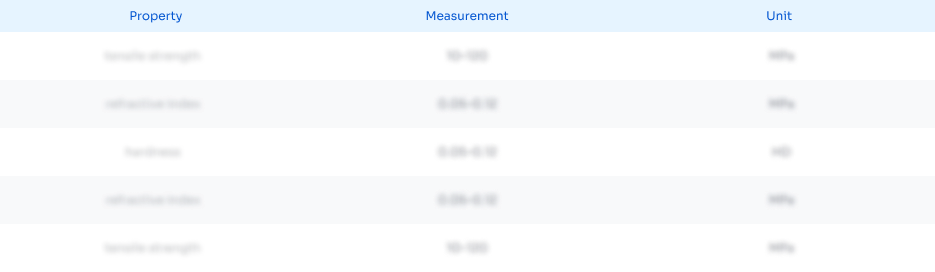
Abstract
Description
Claims
Application Information

- R&D
- Intellectual Property
- Life Sciences
- Materials
- Tech Scout
- Unparalleled Data Quality
- Higher Quality Content
- 60% Fewer Hallucinations
Browse by: Latest US Patents, China's latest patents, Technical Efficacy Thesaurus, Application Domain, Technology Topic, Popular Technical Reports.
© 2025 PatSnap. All rights reserved.Legal|Privacy policy|Modern Slavery Act Transparency Statement|Sitemap|About US| Contact US: help@patsnap.com