Method for separating molybdenum from aluminium in alkaline solution
An alkaline solution and separation method technology, applied in the direction of improving process efficiency, etc., can solve the problems of large adsorption surface area and affecting the separation of molybdenum and aluminum
- Summary
- Abstract
- Description
- Claims
- Application Information
AI Technical Summary
Problems solved by technology
Method used
Image
Examples
Embodiment Construction
[0013] In the alkaline solution containing molybdenum and aluminum, add sodium hydroxide solution to adjust the free alkali concentration; according to the aluminum content of the solution and Al:Si (molar ratio), under stirring at 80rpm, add sodium silicate solution at a uniform speed; After crystallization and crystallization, filter with a centrifuge; the filter cake is stirred and washed with 500mL tap water at 26°C for 30 minutes and then centrifugally filtered to control the moisture content of the filter cake within 20%, and the filtrate is a molybdate solution. The specific technical scheme is shown in Table 1; the obtained results are shown in Table 2.
[0014] The technical solution of the embodiment of table 1
[0015]
[0016] The raw material of table 2 embodiment and test result
[0017]
PUM
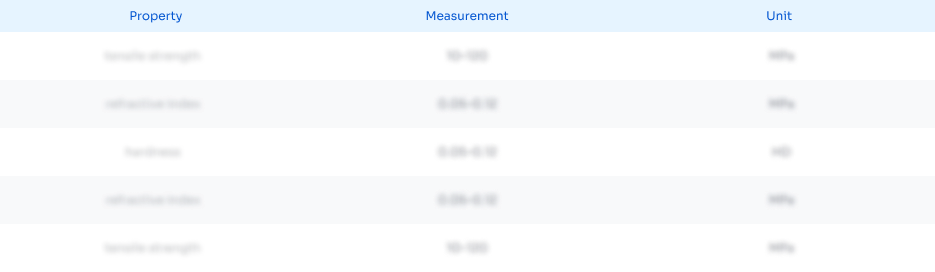
Abstract
Description
Claims
Application Information

- R&D
- Intellectual Property
- Life Sciences
- Materials
- Tech Scout
- Unparalleled Data Quality
- Higher Quality Content
- 60% Fewer Hallucinations
Browse by: Latest US Patents, China's latest patents, Technical Efficacy Thesaurus, Application Domain, Technology Topic, Popular Technical Reports.
© 2025 PatSnap. All rights reserved.Legal|Privacy policy|Modern Slavery Act Transparency Statement|Sitemap|About US| Contact US: help@patsnap.com