A method for extracting and removing molybdenum from tungstate solution
A tungstate and solution technology, applied in the field of solution purification and impurity removal, can solve the problems of volatilization of diluent kerosene, unfavorable industrial application, accelerated extraction agent degradation, etc. Effect
- Summary
- Abstract
- Description
- Claims
- Application Information
AI Technical Summary
Problems solved by technology
Method used
Image
Examples
Embodiment 1
[0023] For the crude sodium tungstate solution containing 249g / L tungsten trioxide and 3g / L molybdenum, add sodium sulfide solution according to the molar ratio of sulfur molybdenum to 3, slowly add ammonium chloride under vigorous stirring to adjust the pH value to 9.5, Sulfurize at 70°C for 0.5 hours, then mix with new organic phase, extract at 25°C for 15 minutes to obtain an extracted organic phase and raffinate, the molybdenum content in the raffinate is 0.52g / L. Add sodium hydrosulfide solution to the above raffinate according to the molar ratio of sulfur and molybdenum to 6, sulfide and react at 70°C for 2 hours, then place the solution at 90°C and vacuum degree of -20kPa for 0.5 hours to volatilize and desulfurize, and use untreated The crude sodium tungstate solution containing 249g / L tungsten trioxide and 3g / L molybdenum added with vulcanizing agent absorbs volatilized volatilizing agent, and it can be observed that the color of the solution turns yellow and gradually...
Embodiment 2
[0026]For the crude ammonium tungstate solution containing 193g / L tungsten trioxide and 15.6g / L molybdenum, add ammonium sulfide solution according to the molar ratio of sulfur and molybdenum to 2, react for 2 hours at 10°C, and then mix with new organic phase , extracted at 10° C. for 30 minutes to obtain an extracted organic phase and a raffinate, and the molybdenum content in the raffinate was 1.52 g / L. Add the above raffinate to the ammonium sulfide solution according to the molar ratio of sulfur and molybdenum to 9, sulfide and react at 10°C for 8 hours, then place the solution at 40°C and vacuum degree of -95kPa for 2 hours to volatilize and desulfurize, and use The crude ammonium tungstate solution containing tungsten trioxide of 193g / L and molybdenum of 15.6g / L absorbs the volatilized vulcanizing agent, and it can be observed that the color of the solution turns yellow and gradually transitions to orange, indicating that volatilized volatilization agent involved in the...
Embodiment 3
[0029] For the crude ammonium tungstate solution containing 171g / L tungsten trioxide and 29.6g / L molybdenum, add ammonium sulfide solution according to the molar ratio of sulfur and molybdenum to 3, vulcanize at 45°C for 2 hours, and then mix with new organic phase , extracted at 40° C. for 15 minutes to obtain an extracted organic phase and a raffinate, and the molybdenum content in the raffinate was 2.18 g / L. The above new organic phase contains 5 wt.% methyltrialkylammonium chloride, 5 wt.% isooctyl alcohol, and 90 wt.% kerosene. Add the above raffinate to the ammonium sulfide solution according to the molar ratio of sulfur and molybdenum to 12, and react for 4 hours at 55°C for sulfidation, then divide the above-mentioned two-stage sulfided liquid into four parts, and one part of the solution is not subjected to vacuum desulfurization treatment. Directly carry out the second-stage extraction molybdenum removal operation; the other three solutions are vacuum desulfurized un...
PUM
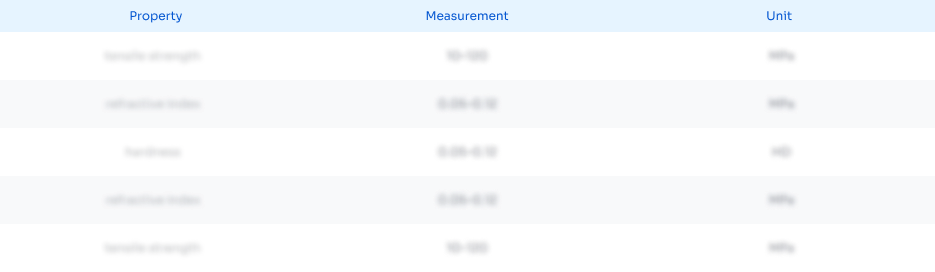
Abstract
Description
Claims
Application Information

- R&D
- Intellectual Property
- Life Sciences
- Materials
- Tech Scout
- Unparalleled Data Quality
- Higher Quality Content
- 60% Fewer Hallucinations
Browse by: Latest US Patents, China's latest patents, Technical Efficacy Thesaurus, Application Domain, Technology Topic, Popular Technical Reports.
© 2025 PatSnap. All rights reserved.Legal|Privacy policy|Modern Slavery Act Transparency Statement|Sitemap|About US| Contact US: help@patsnap.com