Passivation liquid for passivation of electroplating zinc coating and application of same
A technology of passivation solution and electro-galvanizing, which is applied in the coating process of metal materials, etc., to achieve the effect of beautiful color, simple operation and good anti-corrosion performance
- Summary
- Abstract
- Description
- Claims
- Application Information
AI Technical Summary
Problems solved by technology
Method used
Examples
Embodiment 1
[0029] Example 1: HNO 3 Influence of dosage on the performance of passivation liquid
[0030] The formula of passivation solution is: potassium permanganate 2g / L, concentrated nitric acid is 1, 2, 4, 6, 8, 10, 12ml / L (mass concentration 65-68%, the following is the same), sulfuric acid Aluminum 20g / L, sodium nitrate 10g / L, nickel sulfate 10g / L, mixed in deionized water to obtain 1L passivation solution. The operating temperature is room temperature, the galvanized workpiece is immersed in the above passivation solution for 25s, and the residence time in the air is 15s. After drying (or drying), it is immediately aged at 80℃ for about 15min. When the pH is about 7, the temperature is 25-28°C, and the galvanized workpiece is immersed in 5% sodium chloride aqueous solution.
[0031] The result is: for the formula corresponding to concentrated nitric acid 1, 2, 4, 6, 8, 10, and 12ml / L, the corrosion point time of the galvanized workpiece is 6, 18, 46, 72, 52, 20, 8h; In addition, the...
Embodiment 2
[0032] Example 2: KMnO 4 Influence of dosage on the performance of passivation liquid
[0033] The passivation solution formula is: potassium permanganate 0.5, 1, 1.5, 2, 3, 4, 5g / L, concentrated nitric acid 6ml / L, aluminum sulfate 20g / L, sodium nitrate 10g / L, nickel sulfate 10g / L L, mix well in deionized water to get 1L passivation solution. The operating temperature is room temperature, the galvanized workpiece is immersed in the above passivation solution for 25s, and the residence time in the air is 15s. After drying (or drying), it is immediately aged at 80℃ for about 15min. When the pH is about 7, the temperature is 25-28°C, and the galvanized workpiece is immersed in 5% sodium chloride aqueous solution.
[0034] The result is: for the formula corresponding to potassium permanganate 0.5, 1, 1.5, 2, 3, 4, 5g / L, the time of appearance of corrosion points are: 8, 36, 46, 72, 42, 26, 22h; , The passivation film with low potassium permanganate content is thin and the color is ve...
Embodiment 3
[0035] Example 3: AI 2 (SO 4 ) 3 Influence of dosage on the performance of passivation liquid
[0036] The passivation solution formula is: potassium permanganate 2g / L, concentrated nitric acid 6ml / L, aluminum sulfate 0, 5, 10, 20, 30, 40g / L, sodium nitrate 10g / L, nickel sulfate 10g / L, Mix well in deionized water to obtain 1L passivation solution. The operating temperature is room temperature, the galvanized workpiece is immersed in the above passivation solution for 25s, and the residence time in the air is 15s. After drying (or drying), it is immediately aged at 80℃ for about 15min. When the pH is about 7, the temperature is 25-28°C, and the galvanized workpiece is immersed in 5% sodium chloride aqueous solution.
[0037] The result is: for the formula corresponding to aluminum sulfate 0, 5, 10, 20, 30, 40g / L, the time for corrosion point is 24, 42, 60, 72, 70, 64h; in addition, no aluminum sulfate passivation film Rough, uneven color.
PUM
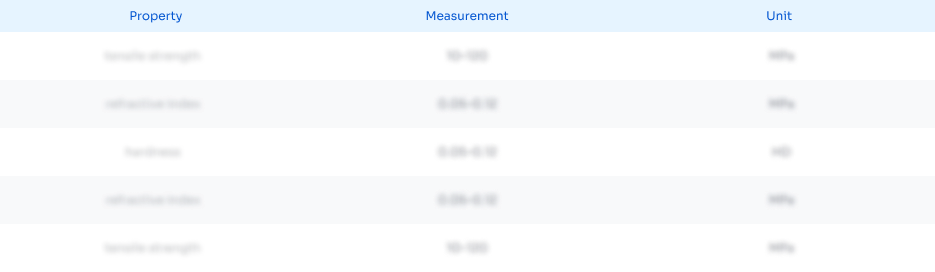
Abstract
Description
Claims
Application Information

- R&D Engineer
- R&D Manager
- IP Professional
- Industry Leading Data Capabilities
- Powerful AI technology
- Patent DNA Extraction
Browse by: Latest US Patents, China's latest patents, Technical Efficacy Thesaurus, Application Domain, Technology Topic, Popular Technical Reports.
© 2024 PatSnap. All rights reserved.Legal|Privacy policy|Modern Slavery Act Transparency Statement|Sitemap|About US| Contact US: help@patsnap.com