Method for improving compressive strength of alkali pellets prepared with limestone
A technology of alkaline pellets and compressive strength, which is applied in the field of improving the compressive strength of pellets mixed with limestone, which can solve the problems such as the decrease of compressive strength of pellets, and achieve the effect of increasing oxidation and improving compressive strength
- Summary
- Abstract
- Description
- Claims
- Application Information
AI Technical Summary
Problems solved by technology
Method used
Image
Examples
Embodiment 1
[0023] Firstly, the limestone is ground to a particle size of 3 μm, and then the ultra-fine limestone powder is mixed into the concentrate powder with a particle size below 74 μm and an iron content of 86%, and the mass percentage is 8:92, and then mixed evenly after mixing. The moisture content of the mixture is controlled at 8.0%. Then carry out pelletizing in disc pelletizing machine, pelletizing time is 10 minutes. After pelletizing, sieve green pellets with a particle size of 8-16mm and dry them at 450°C for 7 minutes, then preheat at 650°C for 15 minutes, and enrich the oxygen during the preheating process, and keep the oxygen content at 14% , the preheated pellets were roasted at a temperature of 1260°C for 15 minutes, the oxygen content was controlled at 12% during the roasting process, and then soaked at a temperature of 1150°C for 3 minutes. After soaking, cool the pellets with air at room temperature to below 150°C to obtain alkaline pellets with a compressive stre...
Embodiment 2
[0025] Firstly, the limestone is ground to 2.5μm, and then the fine-grained limestone powder is added to the concentrate powder with a particle size below 74μm and an iron content of 85%. The mass percentage of limestone powder and concentrate powder is 3:97. Carry out mixing then, the moisture content of mixture is controlled at 7.8%.
[0026] The well-mixed material is pelletized with a disc pelletizer, and the pelletizing time is controlled for 10 minutes. Then use a sieve to sieve green balls with a particle size of 8 to 16 mm for roasting.
[0027] The roasting process includes drying, preheating, roasting, soaking and cooling. The prepared green pellets are first dried at 350°C for 7 minutes, and then preheated at 750°C for 15 minutes. During the preheating process, oxygen is enriched and the oxygen content is kept at 12%. The preheated pellets are heated at 1250°C Calcined at a temperature of 15 minutes, the oxygen content was controlled at 10% during the roasting pro...
Embodiment 3
[0029] Firstly, the limestone is ground to 2μm, and then the superfine limestone powder is mixed into the concentrate powder with a particle size below 74μm and an iron content of 80%. The mass percentage of limestone powder and concentrate powder is selected as 5: 95, then mix and add water, the moisture is controlled at 8.0%.
[0030] The well-mixed material is pelletized with a disc pelletizer, and the pelletizing time is 10 minutes. After pelletizing, use a sieve to sieve green pellets with a particle size of 8 to 16 mm for roasting.
[0031] The roasting process includes drying, preheating, roasting and cooling. The prepared green pellets are first dried at 400°C for 7 minutes, and then preheated at 800°C for 15 minutes. During the preheating process, oxygen is enriched and the oxygen content is kept at 14%. The preheated pellets are heated at 1250°C Calcined at low temperature for 15 minutes, the oxygen content was controlled at 11%, and the calcined pellets were soake...
PUM
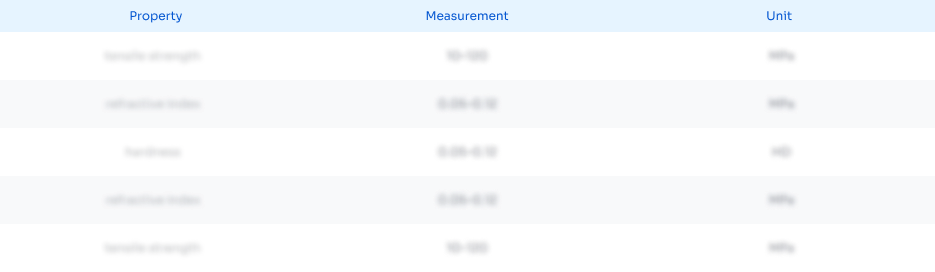
Abstract
Description
Claims
Application Information

- R&D
- Intellectual Property
- Life Sciences
- Materials
- Tech Scout
- Unparalleled Data Quality
- Higher Quality Content
- 60% Fewer Hallucinations
Browse by: Latest US Patents, China's latest patents, Technical Efficacy Thesaurus, Application Domain, Technology Topic, Popular Technical Reports.
© 2025 PatSnap. All rights reserved.Legal|Privacy policy|Modern Slavery Act Transparency Statement|Sitemap|About US| Contact US: help@patsnap.com