Ceramic-polymer composite microwave material as well as preparation method and application methods thereof
A technology of microwave materials and application methods, which is applied in the field of ceramic-polymer composite microwave materials and their preparation and application, can solve the problems of low dielectric constant and high dielectric constant, achieve low microwave loss, and be easy to produce in large quantities Effect
- Summary
- Abstract
- Description
- Claims
- Application Information
AI Technical Summary
Problems solved by technology
Method used
Image
Examples
Embodiment 1
[0025] Using K90 ceramic powder (Ba-Nd-Ti system, dielectric constant 88, BNT for short), after sintering at a temperature of 1280 ℃, planetary ball milling for 30 minutes, drying out, and passing through a 120 mesh sieve. Add n-butyl titanate, which accounts for 2% of the mass of the K90 powder, after grinding and mixing, aging in a sealed bag for 24 hours for later use.
[0026] The commercial polystyrene (PS) is ultrasonically cleaned with alcohol and dried. Weigh PS and stale BNT powder according to the weight ratio of 25:205. Put the weighed PS into 150ml xylene solvent, stir and dissolve at 80℃, then add the BNT powder weighed in proportion, heat up to 120℃, continue stirring, until the xylene solvent is distilled and recovered. The powder obtained is crushed and passed through a 60-mesh sieve twice. The obtained powder: the volume content of PS is 40%, and the volume content of BNT is 60%.
[0027] The commercial powdered high-density polyethylene (HDPE) is ultrasonically...
Embodiment 2
[0031] Using K90 type powder (Ba-Nd-Ti system, dielectric constant 88, BNT for short), after sintering at a temperature of 1280 ℃, planetary ball milling for 30 minutes, drying out, and passing through a 120 mesh sieve. Add n-butyl titanate, which accounts for 2% of the mass of the K90 powder, after grinding and mixing, aging in a sealed bag for 24 hours for later use.
[0032] The commercial low-density polyethylene (LDPE) is ultrasonically cleaned with alcohol and dried. Weigh the LDPE and stale BNT powder at a weight ratio of 1.5:100. Put the weighed LDPE into the xylene solvent, stir and dissolve at 80°C, then add the weighed BNT powder, raise the temperature to 120°C, and continue stirring until the xylene solvent is distilled and recovered. The powder obtained is crushed and passed through a 60-mesh sieve twice.
[0033] The commercial powdered high-density polyethylene (HDPE) is ultrasonically cleaned with alcohol and dried. Mix with the BNT powder prepared in the previou...
PUM
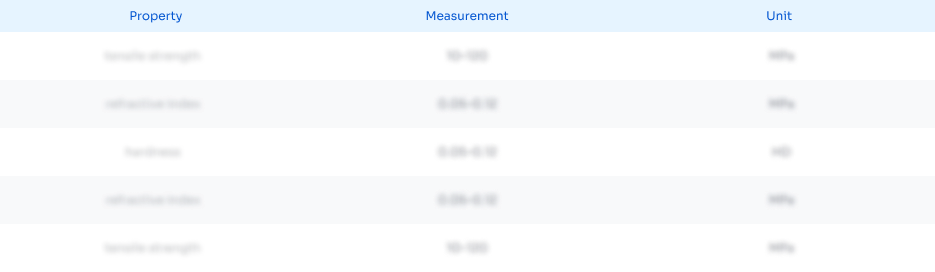
Abstract
Description
Claims
Application Information

- Generate Ideas
- Intellectual Property
- Life Sciences
- Materials
- Tech Scout
- Unparalleled Data Quality
- Higher Quality Content
- 60% Fewer Hallucinations
Browse by: Latest US Patents, China's latest patents, Technical Efficacy Thesaurus, Application Domain, Technology Topic, Popular Technical Reports.
© 2025 PatSnap. All rights reserved.Legal|Privacy policy|Modern Slavery Act Transparency Statement|Sitemap|About US| Contact US: help@patsnap.com