Preparation method of polyester hot melt adhesive with good weather resistance
A technology of polyester hot melt adhesive and weather resistance, applied in the direction of adhesives, etc., can solve the problems of brittleness, difficult operation, hot melt adhesive does not have anti-ultraviolet aging, etc.
- Summary
- Abstract
- Description
- Claims
- Application Information
AI Technical Summary
Problems solved by technology
Method used
Image
Examples
Embodiment 1
[0023] 134.5 g (0.81 mol) of terephthalic acid, 89.6 g (0.54 mol) of isophthalic acid, 30.3 g (0.15 mol) of sebacic acid, 189 g (2.1 mol) of 1,4-butanediol, tetratitanate Add 0.10 g of butyl ester and 0.18 g of butyl stannoic acid into a 1 L reaction flask with a distillation device. Gradually raise the temperature to 90°C and start stirring, then rise to 170°C, water begins to distill out, continue to heat up to 210°C, when the distilled amount of water reaches 94% of the theoretical amount, the esterification reaction ends. Add 1.25 g of antioxidant tetraerythritol ester, light-stabilized
[0024] 0.25 g of 4-benzoyloxy-2,2,6,6-tetramethylpiperidine and 1.5 g of nucleating agent talcum powder were used for compression polymerization under reduced pressure. The temperature was raised to 250 °C and the reaction pressure was kept at 100 ~ 140 Pa, react for about 80 minutes, and discharge to obtain copolyester E1.
[0025]
Embodiment 2
[0027] 117.0 g (0.70 mol) of terephthalic acid, 117.0 g (0.70 mol) of isophthalic acid, 18.2 g (0.09 mol) of sebacic acid, 202.5 g (2.25 mol) of 1,4-butanediol, tetratitanate Add 0.076 g of butyl ester and 0.20 g of butyl stannoic acid into a 1 L reaction flask with a distillation device. Gradually raise the temperature to 90°C and start stirring, then rise to 170°C, water begins to distill out, continue to heat up to 210°C, when the distilled amount of water is more than 94% of the theoretical amount, the esterification reaction ends. Add antioxidant tetraerythritol ester 1.26 g, light stabilizer 4-benzoyloxy-2,2,6,6-tetramethylpiperidine 0.25 g and talcum powder 1.5 g to carry out reduced-pressure compression polymerization. 245 ℃, keep the pressure in the reaction bottle at 80 ~ 120 Pa, react for about 100min, and discharge to obtain copolyester E2.
Embodiment 3
[0029] 119.5 g (0.72 mol) of terephthalic acid, 97.1 g (0.585 mol) of isophthalic acid, 39.4 g (0.195 mol) of sebacic acid, 216 g (2.4 mol) of 1,4-butanediol, tetratitanate Add 0.10 g of butyl ester and 0.13 g of butyl stannoic acid into a 1 L reaction flask with a distillation device. Gradually raise the temperature to 90°C and start stirring, then rise to 170°C, water begins to distill out, continue to heat up to 210°C, when the distilled amount of water is more than 94% of the theoretical amount, the esterification reaction ends. Add antioxidant tetraerythritol ester 1.28 g, light stabilizer 4-benzoyloxy-2,2,6,6-tetramethylpiperidine 0.25 g and talcum powder 1.5 g to carry out reduced-pressure compression polymerization. 250 ℃, keep the pressure in the reaction bottle at 80 ~ 100 Pa, react for about 70 minutes, and discharge to obtain copolyester E3.
[0030]
PUM
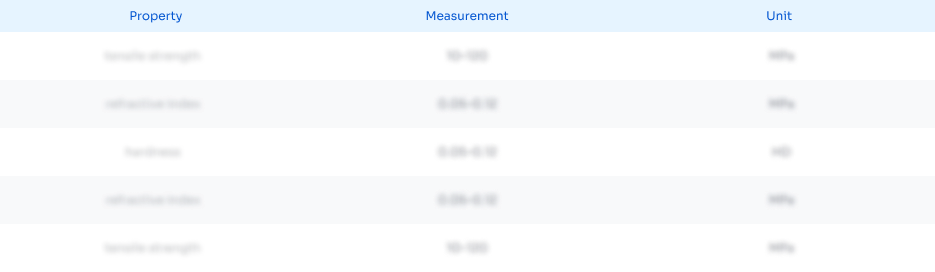
Abstract
Description
Claims
Application Information

- R&D Engineer
- R&D Manager
- IP Professional
- Industry Leading Data Capabilities
- Powerful AI technology
- Patent DNA Extraction
Browse by: Latest US Patents, China's latest patents, Technical Efficacy Thesaurus, Application Domain, Technology Topic, Popular Technical Reports.
© 2024 PatSnap. All rights reserved.Legal|Privacy policy|Modern Slavery Act Transparency Statement|Sitemap|About US| Contact US: help@patsnap.com